Guide to 3D Printed Masking Tools For Painting, Coating, and More
Masking, or the strategic covering of certain areas during a processing step such as painting, media blasting, or metalizing, is traditionally a labor-intensive step in manufacturing processes with a low margin for error. 3D printing presents a cost-effective means of creating customized masking parts that can fit complex geometries and be used repeatedly, reducing the need for hours of manual labor during post-production workflows.
Both stereolithography (SLA) and selective laser sintering (SLS) 3D printing technologies can be used in the manufacturing of masking tools, and each presents unique advantages. In this guide, we will outline the considerations to take when creating masks, how to evaluate which 3D printing technology is right for your workflow, and provide examples of customers successfully finishing their parts with the help of 3D printed masks.
What Is Masking?
Masking is the strategic covering of certain areas on a part that need to remain free of any coating, painting, metallizing, or other surface finishing processes. Those areas may need to remain untouched for various reasons — because they will become an attachment area for an assembly, for electrical conductivity reasons, or because they might need to be coated in some other material or color, among others. Masks are therefore manufacturing aids that can be customized and made to correspond to each final part, or created once and used as each part goes through the finishing process individually.
Even in industries where much of the finishing process is automated, like in the automotive industry, masking is still often done by hand with tape and paper. Photo credit: mirka.com
How Are Masking Tools Made?
Traditional masking workflows include manually measuring and cutting masking tape, machining metal or plastic masks, or sometimes coating an entire part and then machining or scraping away the coating from the designated area. Taping workflows, though they use cheap materials, are extremely labor-intensive, and can add minutes of labor time per part on a production line. Machined masks can be repeatedly used but are expensive to manufacture, and the machining process confers some geometric limitations.
Masks are an ideal application for 3D printing — they are often needed in low-volume production quantities and with very specific geometries to ensure they only cover certain areas at the center, on the edges, or in a specific pattern across a larger part. 3D printed masks can be produced with less labor, offer more repeatability, and simplify many complex masking jobs, or be used as masking prototypes to validate workflows before moving to another material.
3D Printing Masking Considerations
There are a few factors to consider when selecting a material option for producing masks. These factors are mechanical and chemical requirements, part fit, and production requirements.
-
Temperature: This is the largest limiting factor, as some coatings cure at temperatures above in ovens or kilns. For many lower-temperature powder coating processes, High Temp Resin can withstand up to 238° C.
-
Abrasiveness: Some finishing processes use abrasive mediums and the masks need to be made from materials that can withstand the forces of the media used, like ceramic pellets or walnut shells. For these instances, use a harder material such as Rigid 10K Resin for SLA parts or Nylon 12 GF Powder for SLS parts.
-
Solution Use: Many coatings require solutions, both basic and acidic. If an acidic or basic solution is part of the processing workflow, make sure to compare the TDS with the chemical requirements.
-
Part Fitment: When pressing a mask onto a part, different amounts of stiffness or flexion are needed in different scenarios. 3D printing makes it easy to try multiple materials at a low cost, like Durable Resin or Rigid 10K Resin, or Nylon 11 Powder and Nylon 12 Powder.
-
Production Requirements: Some masking applications require only one or two masks, while others need to match the volume of masks to the volume of parts. Formlabs’ SLA printers, both Form 3+ and Form 3L, are great choices for low volumes of masks, such as subtractive processes that can only be done a few at a time. The Fuse 1+ 30W SLS printer is better suited for higher volumes of masks given its ability to vertically stack multiple parts within the same build.
SLA and SLS Technologies for Masking
SLA: Form 3+ and Form 3L
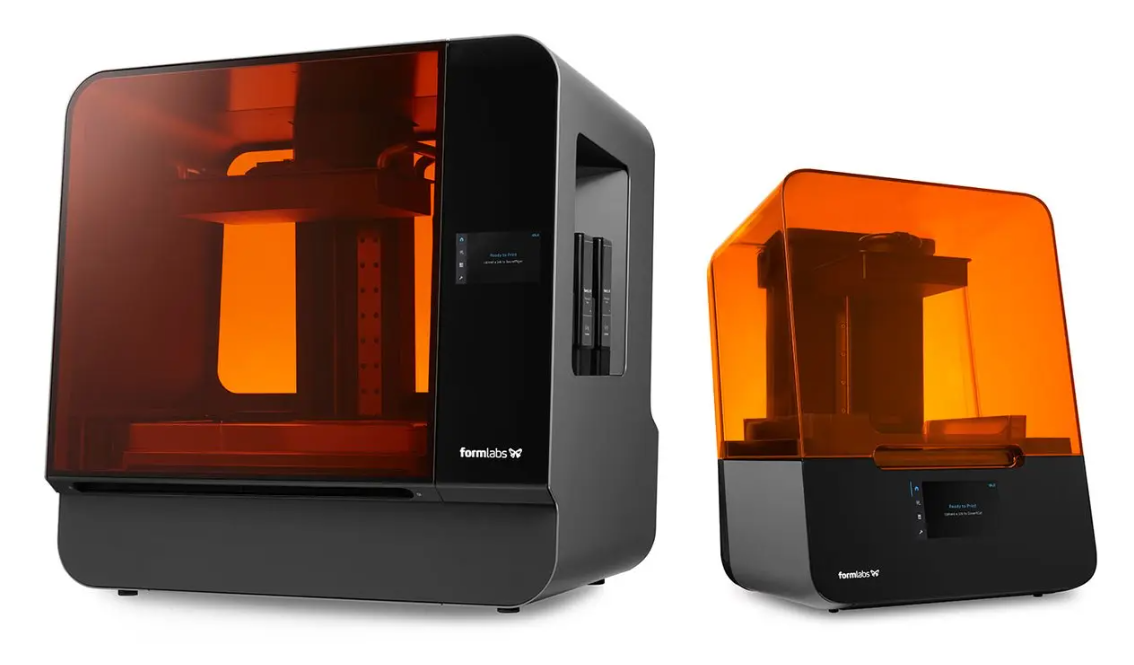
Formlabs SLA printers, the Form 3+ desktop and Form 3L benchtop units, offer a broad range of material options, quick turnaround time, high resolution, and large-format capacity. The versatility of the Formlabs SLA printers is another advantage — with over 40 resins to choose from, users can select a material uniquely suited to their material property needs. The resins range from soft, compliant materials like Elastic 50A Resin for a mask that simulates silicone, to Rigid 10K Resin for stiff, rigid masks. For masking process considerations like temperature or conductivity, the Formlabs materials library offers specialized materials as well, like ESD Resin to effectively dissipate electrostatic discharge.
RESIN | KEY STRENGTH | HDT |
---|---|---|
Draft Resin | Very high print speed. This resin is a great choice for quick turnaround when tolerance is not a primary concern. | 57 ℃, 135 ℉ |
Durable Resin | Compliant and high impact strength. A good material choice when looking for snug fits, press fits, or flex/conformity around features. | 41℃, 106℉ |
Tough 1500 Resin | Stiffer than Durable Resin while still maintaining compliance. | 52℃, 126℉ |
Rigid 10K Resin | Very stiff resin, great choice for masking applications where slide fittings or sharp edges are desirable. Can also be a good selection for abrasive processes. | 218℃, 424℉ |
High Temp Resin | Formlabs’ highest temperature resin, High Temp Resin is an option for any processes requiring temperature cures. | 238℃, 460℉ |
Elastic 50A Resin | Lowest durometer material. Elastic 50A is a good option when compliance is the primary concern. |
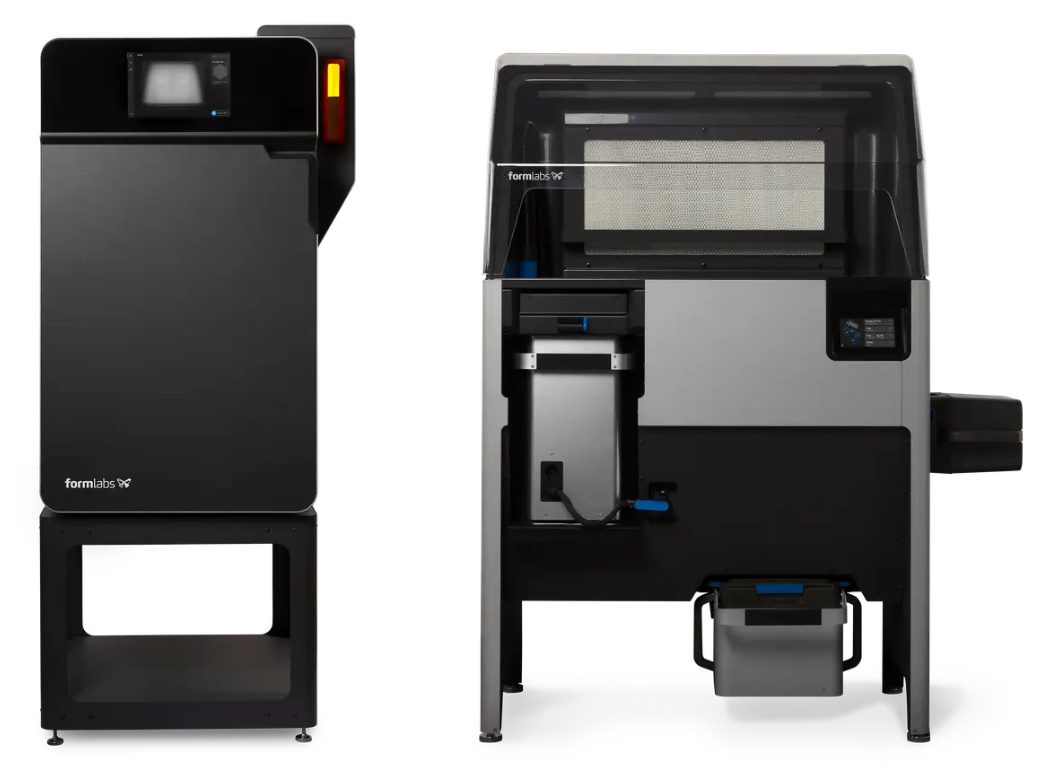
Formlabs SLS Powders, which include four types of nylon and one TPU powder, are well known in manufacturing disciplines, and can be relied upon for durable strength and ruggedness.In general nylon materials have good chemical compatibility performance. Due to its semi-crystalline structure, Nylon materials have good resistance to petroleum, acetone, and silicone-based greases, and are less susceptible to environmental stress cracking.
POWDER | KEY STRENGTH | HDT |
---|---|---|
Nylon 12 Powder | Lowest price SLS material option with a high refresh rate, stiffer and higher HDT under force than Nylon 11 with better flexural strength. If the masks require a stiff component or to minimize production costs, select Nylon 12 Powder. | 171℃, 340℉ |
Nylon 11 Powder | High performance material with great impact strength, good performance on thin features, and a high degree of ductility. Nylon 11 is a great choice for SLS compliant masks or masks requiring very fine features. | 182℃, 360℉ |
Nylon 11 CF Powder | 188℃, 370℉ | |
TPU 90A Powder | An elastomeric SLS material, allowing for flexible components with a high degree of design freedom. TPU can be used for gasketings, plugs, and compliant masks. | 94℃, 202℉ |
NIC Industries, the manufacturer of Cerakote, has been coating 3D printed parts and using 3D printed masks for a long time, and find them especially useful when deploying their robotic Cerakoting machine for high volume production.
For a batch production run of sample parts, they worked with Formlabs to produce 1,000 units, using SLS 3D printed masks to quickly and efficiently mask certain surfaces. Masks were printed using Nylon 12 Powder on the Fuse 1+ 30W SLS printer, and served to cover the inside of the two-part final product assembly to prevent overspraying and ensure clean delineation between colors. The masks also serve to fixture the part to the robotic applicator assembly, allowing for high throughput, and consistent coating.
SLS 3D printed mask and fixture (left), 3D printed masks fixtured to allow for robotic coating (center), and two-piece SLS 3D printed sample part, finished with Cerakote H-Series (right).
On another part, NIC industries needed to post-process this bow riser, but protect the inner channel of a screw thread during the coating phase before final assembly. Prior to having Cerakote applied, NIC Industries designed and 3D printed a mask to protect interior surfaces of this bow riser. They designed a plug-style mask that fits into the screw thread and prevents any coating material from entering the cavity to ensure a smooth threading in the final assembly. The plugs can be easily removed, flex slightly to pop in and out of the cavity, and are durable enough to be used for hundreds of coating applications.
Nylon 12 Powder two-piece 3D printed mask for bow riser
Bow riser and 3D printed mask assembled
3D Printed Masks Reduce Costs and Improve Aesthetics and Performance
3D printing masks in-house can reduce labor costs, improve the look and performance of final parts, and streamline validation processes. The use of 3D printed parts in end-use applications is growing, and coating, dyeing, and painting are often necessary steps. Masking tools are necessary for both these 3D printed parts, and for many traditionally manufactured items. The advantages that 3D printing provides for the part itself (customization, design freedom, affordability of low volume production) also apply to the fabrication of the masks. Leveraging the speed, efficiency, and material versatility of Formlabs SLA and SLS printers can streamline in-house masking fabrication and reduce bottlenecks in your supply chain.
To learn more about which Formlabs 3D printer and material are best suited to your application for masking, contact our sales team.
Wil je nooit onze blogs missen?
/dennie-rijk-spreker-layertec.jpg?width=80&height=80&name=dennie-rijk-spreker-layertec.jpg)