Hoe Tessy Plastics de downtime vermindert met de Fuse 1
Transformeren van voedselverwerkingsapparatuur
Elliði Hreinsson heeft Curio opgericht en uitgebouwd tot een topproducent van verwerkingsmachines voor het ontkoppen, fileren en villen van vis. Curio is het bedrijf dat verschillende 3D metaalprinters van Desktop Metal en ETEC 3D-printers gebruikt om flexibel en innovatief te blijven en werd onlangs overgenomen door Marel (NASDAQ:MAREL), een wereldwijde leider in de ontwikkeling en productie van gereedschappen, complete oplossingen, software en diensten voor de voedselverwerking van kip, vlees en vis.
Met een knipoog naar de sterke IJslandse roots van het bedrijf en de oprichter, ontwikkeld Curio machines die aansluiten bij de behoeften van elk visverwerkingsscenario binnen deze sector. "Wat deze machines onderscheidt, is de nabijheid van het bedrijf bij de industrie", aldus Hreinsson. "We kennen de vis, we kennen de omgeving, we weten hoe we moeten ontwerpen voor het beste resultaat voor de vis."
Na de overname door Marel, blijft Hreinsson werken als adviseur bij het bedrijf. Voortdurend kijkt hij naar het ontwikkelen van duurzame visverwerkingsmachines om zowel de duurzaamheid als gebruik en snelheid te verbeteren, maar ook als leverancier in het produceren van onderdelen via zijn bedrijf Gullmolar.
Hreinsson gebruikte innovatie en vindingrijkheid om onderdelen te ontwerpen en te bouwen die niet beschikbaar waren om de beste voedselverwerkingsproducten op de markt te brengen. "Die motoren werden intern gemaakt", zegt hij tijdens een rondleiding door de Curio-prototyping afdeling. Met productiecapaciteiten zoals CNC-draaibanken en -molens, vijf asbewerking, watersnijden, robotbuigen en lassen, is Hreinsson altijd op zoek naar het meest efficiënte proces om zijn ontwerpen in productie te brengen.
Hij is al enthousiast over de mogelijkheden van Additive Manufacturing sinds zijn eerste kennismaking in de jaren negentig, toen een vriend een gipsen 3D-printer kocht voor het gieten van mallen - hij geeft toe dat de ontwerpen rudimentair waren, maar de mogelijkheden leken eindeloos. Hij integreerde Additive Manufacturing in zijn prototype-activiteiten in 2010 toen hij zijn eerste FDM-achtige 3D-printers kocht. "Er was een nieuw gereedschap in mijn gereedschapskist, er ging een deur open naar nieuwe mogelijkheden," zei hij.
"[Laser powder bed fusion printers] waren altijd verschrikkelijk duur en het onderdeel had achteraf veel nabewerking nodig achteraf, dus ik zag de voordelen niet echt." Elliði Hreinsson, oprichter van Curio en Gullmolar
Maar om de voordelen van Additive Manufacturing echt te benutten voor de productie van Curio machines, moest het bedrijf in staat zijn om metalen 3D onderdelen te printen en dan met name roestvrijstalen onderdelen. "Ik keek altijd naar laserbed fusieprinters," zei Hreinsson. "Ik zag ook een aantal in actie, maar ze waren altijd verschrikkelijk duur en het onderdeel had achteraf veel nabewerking nodig, dus ik zag de voordelen niet echt."
Na het ontdekken van de Bound Metal Deposition technologie van Desktop Metal, was Hreinsson ervan overtuigd dat hij de sleutel had gevonden om nieuw potentieel te ontsluiten voor zijn producten, onderdelen en machines. In tegenstelling tot laser gebaseerde systemen die los metaalpoeder smelten met strikte facilitaire vereisten, extrudeert het Studio System gebonden metalen staven die Additive Manufacturing mogelijk maakt in een kantoorvriendelijke omgeving. Hij investeerde in twee Studio System 3D printers om 316L roestvrijstalen toepassingen te produceren en een Desktop Metal Furnace om de builds te sinteren en dichte metalen onderdelen te produceren.
Met ervaring in traditionele CNC-processen gaf Hreinsson toe dat hij de diktes van zijn eerste prints heeft verhoogd tot boven de ontwerprichtlijnen, omdat 3D metaalprinten onbekend en moeilijk te vertrouwen was in zijn optiek. "Ik was sceptisch over de sterkte van het materiaal. Maar met meer ervaring besefte ik dat we de wanddikte zonder reden verhoogden wat eigenlijk alleen maar zorgde voor meer materiaal en sintertijd," zei hij lachend.
Het tweestappenproces van het Studio System en de Desktop Metal Furnace, gewoon printen en sinteren, leverde onmiddellijke voordelen op voor de innovatie van de Curio machines.
Na het realiseren van de quick-turn mogelijkheden om onderdelen on-demand te produceren en te itereren, werden twee extra Studio Systems en een tweede oven toegevoegd aan de productiefaciliteiten van Gullmolar. Hreinsson voegde ook digitale licht processing (DLP) machines van ETEC, Desktop Metal's merk van polymeer 3D printers, toe. Deze range aan 3D printers zorgt ervoor dat hij de klok rond 3D onderdelen kan printen.
Aan de Michigan State University College of Veterinary Medicine komen patiënten in alle vormen, maten en soorten binnen. Voor Dr. Danielle Marturello, DVM, MS, DACVS, Assistant Professor of Small Animal Orthopedic Surgery (Assistent Professor Orthopedische Chirurgie bij Kleine Dieren), betekent dit dat elke dag anders is. Op sommige dagen is ze in de kliniek en ziet ze honden en katten met botbreuken, misvormingen van het skelet of scheuren van de gewrichtsbanden. Op een andere dag is ze in de operatiekamer om deze patiënten te helpen herstellen en hen weer gezond te maken.
Thunder, een MSU veterinaire orthopedische patiënt, tijdens een controle.
Verschillende patiënten, verschillende uitdagingen
In de veterinaire orthopedie moeten artsen de opbouw en structuur van niet één, maar vele skeletsystemen uit hun hoofd leren. Om haar team te helpen bij het visualiseren, plannen en uitvoeren van complexe operaties, maakt Dr. Marturello gedetailleerde 3D-modellen en chirurgische gidsen van beeldgegevens met behulp van een vloot Formlabs stereolithografie- (SLA-) printers. De verscheidenheid aan beschikbare materialen betekent ook dat de printers leermiddelen kunnen maken voor veterinaire studenten, stagiaires en assistenten. Dit bevordert de chirurgische resultaten en educatieve ervaring die MSU kan bieden.
Complexe gevallen oplossen met hoogwaardige beeldvorming
Net als bij de menselijke geneeskunde is de veterinaire orthopedie sterk afhankelijk van kwaliteitsbeelden. Bij een patiënt zal Dr. Marturello altijd op zijn minst een röntgenfoto opvragen. Daarna, afhankelijk van de complexiteit van de zaak en of er al dan niet een 3D-model nodig is, eventueel een aanvullende CT-scan. In tegenstelling tot de menselijke geneeskunde, zijn deze patiënten niet in staat om hun pijnniveau of pijnlocatie door te geven. Daarom zijn beeldvorming en modellering met hoge resolutie nog belangrijker voor zowel de diagnose als de behandeling, samen met een grondig lichamelijk onderzoek.
"Beeldvorming is essentieel voor onze carrière en ons werk. Wanneer we een operatie moeten plannen, wanneer we klaar zijn met een operatie en moeten zien of een implantaat op de juiste plaats zit, eerlijk gezegd kunnen we ons werk niet uitvoeren zonder beeldvorming," aldus Marturello.
Scooby, een patiënt die behandeld wordt voor een angulaire misvorming.
Scooby's aangetaste gewricht, getoond in PreForm voordat het werd geprint.
Deze beelden en modellen worden gebruikt om verschillende pathologieën te bekijken, bijvoorbeeld breuken veroorzaakt door auto-ongevallen, of groeivervormingen waarbij twee botten verkeerd gegroeid zijn en het bewegingsbereik of de normale functie belemmeren. Het team van Dr. Marturello print modellen van de botten in White Resin op de Form 3- of Form 3L-printers om de pathologie te bestuderen en de operatie vooraf te oefenen.
"We moeten er zeker van zijn dat we vooruit plannen - gaat wat we dachten dat zou werken, ook echt werken? We kunnen het ook gebruiken om onze implantaten voor te vormen op dat modelbot, het te steriliseren en dan het voorgevormde implantaat tijdens de operatie te gebruiken, wat tijd bespaart voor de patiënt onder narcose", zegt Marturello.
In een bijzonder gecompliceerd geval werd een hond binnengebracht met een verbrijzeld scheenbeen, zeer dicht bij de knie. Omdat de breuk zo dicht bij het gewricht zat, was het moeilijk om op een röntgenfoto de volledige omvang van de schade te zien. Dr. Marturello printte het gebroken scheenbeen met White Resin op de Form 3, steriliseerde de modellen en maakte ze veilig om mee te nemen naar een operatiekamer.
Dr. Marturello: "We konden tijdens de operatie om het bot heen draaien om een tastbaarder driedimensionaal beeld van het breukenpatroon te krijgen. Dat is belangrijk, omdat we met onze chirurgische aanpak maar één kant zien. Dat geprinte bot was, vanwege de hoek van de breuk, zeer nuttig en hoewel het een heel moeilijk geval was, deed de hond het fantastisch. Het helpt echt om deze operatie naar een hoger niveau te tillen."
In een ander geval was een breuk bij een hond niet goed genezen, waardoor een zogeheten 'non-union'-breuk (pseudartrose) ontstond en de hond niet goed kon lopen. Omdat het zo dicht bij een gewricht was, moest Dr. Marturello een implantaat gebruiken dat een externe fixator wordt genoemd. Echter door de plaats van de breuk pasten de typische pinnen die worden gebruikt om het implantaat aan het bot te bevestigen niet. De oplossing was een ringcomponent en Dr. Marturello oefende eerst op een geprint bot en plaatste de hybride constructie op het model voordat de hond binnenkwam.
De hybride externe fixator gebruikt om de non-union-fractuur hersteloperatie te plannen.
"Toen ik eenmaal de fixator op het geprinte bot had gemaakt, ging alles sneller. Ik kon die constructie van tevoren bestuderen en dan tijdens de operatie gewoon repliceren wat ik op het model had gedaan, wat veel gemakkelijker was," aldus Marturello.
Dr. Andrew Kanawati is orthopedisch en wervelkolomchirurg in het Westmead Hospital in Sydney, met een bijzondere belangstelling voor klinische en onderzoekstoepassingen van 3D-printen. Hij heeft verschillende op maat gemaakte 3D-geprinte, patiënt-specifieke wervelkolomgeleiders ontwikkeld om te helpen bij operaties. Hij gebruikt samengestelde modellen van verschillende Formlabs-materialen voor het plannen van complexe operaties. Dr. Kanawati staat aan de voorhoede van spinale chirurgische innovatie en gebruikt 3D-printen om de resultaten te verbeteren. In deze blog herhalen we enkele van de belangrijkste bevindingen van dr. Kanawati's presentatie tijdens de Formlabs User Summit.
Patiënt-specifieke anatomische modellen kunnen helpen bij operatiesimulaties, discussies binnen het team, gesprekken over de toestemming van de patiënt en de bijbehorende kosten van operaties.
3D-printen van tumoren
In het verleden werd er onderzoek gedaan naar medisch printen gericht op FDM-printers (Fused Deposition Modeling) vanwege hun lage prijs en alomtegenwoordige marktaanwezigheid in de oudere jaren. Dr. Kanawati zag echter een enorme kans om stereolithografie (SLA) te gebruiken vanwege de hoogwaardige materiaaleigenschappen van de uiteindelijke onderdelen. Deze materiaaleigenschappen, waaronder de mogelijkheid om waterdichte onderdelen te printen, betekenden dat medische onderdelen van hogere kwaliteit konden worden geprint en getest.
Op een dag onderzocht dr. Kanawati een 41-jarige patiënt die klaagde over pijn in zijn been. Bij de patiënt was op jonge leeftijd een goedaardige bottumor in zijn bekken vastgesteld, die sindsdien niet-operatief werd behandeld. Uit een nieuwe MRI- en CT-scan bleek dat de tumor naar de zijkant van de wervelkolom van de patiënt groeide. De tumor zat tegen zenuwen aan en vormde een ernstige medische uitdaging.
Elke tumor is anders, en elke patiënt is anders. Voor complexe gevallen waarbij het ruggenmerg en de zenuwen betrokken zijn, kan het onderzoeken van de menselijke anatomie in 3D het verschil betekenen tussen een geslaagde of een mislukte operatie.
Dr. Kanawati ging aan de slag met zijn Formlabs SLA-printer en Grey Resin en begon te printen. Voor een volledig model van de onderrug en de tumor werd 156 ml resin gebruikt, ter waarde van slechts 23 euro. Kanawati: "Grey Resin is het werkpaard van Formlabs. Het heeft een zeer mooie oppervlakte afwerking. Ik vind Grey Resin zeer betrouwbaar in termen van printsucces."
Het ruggengraatmodel van de patiënt werd in iets minder dan 13 uur geprint waarbij slechts 23 euro aan resin werd gebruikt.
De voordelen van 3D printen
Een fysiek 360º model van de wervelkolom en de tumor van de patiënt helpt chirurgen om fouten te verminderen en de resultaten voor de patiënt te verbeteren. De modellen helpen chirurgen de contactpunten tussen de tumor en de zenuwtakken te visualiseren en hanteren, waardoor ze meer handigheid en vertrouwen krijgen bij het opereren. Dit is een belangrijk voordeel van 3D-printen voor spinale chirurgie. Met SLA-printers in huis kunnen chirurgen binnen een dag modellen scannen, segmenteren en printen. In noodgevallen waar tijd van essentieel belang is, kan een 3D-geprint model chirurgen helpen bij hun beslissingen en hen extra vertrouwen geven.
De toegang tot een 3D-geprint model helpt bij de preoperatieve planning, waardoor Dr. Kanawati kan beoordelen of een kortere operatie mogelijk is. Minder operatietijd betekent minder spanning op het ruggenmerg zonder directe neurale schade te veroorzaken. Het geeft het team ook een beter inzicht in welke pedikels (een zeer sterke, cilindrische, anatomische brug tussen de dorsale wervelelementen en het wervellichaam) levensvatbaar zijn, en hoe de operatie het best kan worden uitgevoerd.
Zenuwen werden geprint in Elastic Resin en op het 3D-printbeen geplaatst.
Maar dr. Kanawati was nog niet klaar met het creëren van zijn patiëntenmodel. Hij tilde zijn 3D-printen naar een hoger niveau en toonde de kracht van SLA-printen voor medische toepassingen door met meerdere materialen op één machine te printen. Dr. Kanawati verwisselde zijn build tray voor een nieuwe, en begon met het maken van replica's van de zenuwen van de patiënt in Elastic Resin. Zo kon hij de zenuwen op zijn ruggengraatmodel leggen, zodat er geen verrassingen waren toen de operatie begon. Kanawati: "Tijdens de operatie gingen we via de rug van de patiënt naar binnen. Tijdens de operatie konden we de zenuwen niet zien, maar door het 3D-geprinte model wisten we precies waar ze zaten."
Dat een 3D-printer een "hoge resolutie" heeft in de printerspecificaties betekent niet dat jouw 3D-geprinte onderdelen nauwkeurig of precies zullen zijn. Inzicht in de betekenis van nauwkeurigheid, precisie en tolerantie is noodzakelijk om zinvolle 3D-printprestaties te bereiken voor elke toepassing. In dit blogartikel gaan we dieper in op de betekenis van deze termen in de context van 3D-printen.
Definiëren van nauwkeurigheid, precisie en tolerantie
Laten we beginnen met definities: wat is het verschil tussen nauwkeurigheid, precisie en tolerantie? Voor elke term gebruiken we een schietschijf - een veelgebruikt voorbeeld om deze concepten uit te leggen - om de betekenis te visualiseren.
De nauwkeurigheid binnen 3D printing
Nauwkeurigheid is hoe dicht een meting bij de werkelijke waarde ligt. In het geval van een schietschijf is de werkelijke waarde de roos. Hoe dichter je bij de roos komt, hoe nauwkeuriger jouw schot. In de wereld van 3D-printen is de werkelijke waarde gelijk aan de afmetingen die je in CAD ontwerpt. Hoe dicht komt de 3D-print bij het digitale ontwerp?
De precisie binnen 3D printing
Precisie meet de herhaalbaarheid van een meting: hoe consistent zijn jouw schoten op het doel? Precisie meet alleen deze consistentie; jouw schoten kunnen elke keer op dezelfde plek terechtkomen, maar dat hoeft niet de roos te zijn. Bij 3D-printen komt dit uiteindelijk neer op betrouwbaarheid; kun je erop vertrouwen dat jouw machine bij elke print de verwachte resultaten oplevert.
In algemene technische termen meet "precisie" doorgaans de herhaalbaarheid. Bij het vergelijken van 3D-printmaterialen kan "precies" verwijzen naar materialen die zeer ingewikkelde geometrieën kunnen printen. Formlabs Grey Pro Resin en Rigid Resin hebben bijvoorbeeld een hoge groene modulus, of stijfheid, waarmee dunne, ingewikkelde vormen kunnen worden geprint.
De tolerantie binnen 3D printing
Hoe precies moet je zijn? Dat wordt bepaald door de tolerantie, en jij bepaalt de tolerantie. Hoeveel speelruimte heb je in jouw toepassing? Wat is een aanvaardbare variatie in de nauwkeurigheid van de meting? Dat hangt af van jouw project. Zo zal een component met een dynamische mechanische assemblage nauwere toleranties vereisen dan een eenvoudige plastic behuizing.
Als je een tolerantie definieert, wil je waarschijnlijk ook nauwkeurigheid. Laten we dus veronderstellen dat we de precisie van het schieten op de roos meten. Eerder definieerden we de schoten op het doel rechts als niet precies.
Als je tolerantiebereik echter vrij groot is, kan het alsnog goed zijn. De schoten liggen niet zo dicht bij elkaar als in het doel links, maar als het aanvaardbare precisiebereik de afstand van ±2,5 ringen is, dan zit je binnen de specificaties.
In het algemeen betekent het bereiken en handhaven van nauwere toleranties hogere fabricagekosten en kwaliteitsborging.
3D-printen heeft de afgelopen jaren een flinke groei doorgemaakt. De ontwikkelingen in de 3D-printindustrie hebben een technologie die ooit onbetaalbaar was veel intuïtiever gemaakt voor leraren en studenten. Deze technologie heeft een groot aantal industrieën veranderd, zoals de techniek, productie, tandheelkunde, gezondheidszorg, entertainment, juwelen, audiologie en onderwijs. En nu is het tijd voor scholen om 3D-printen te omarmen, zodat de studenten van vandaag de pioniers van morgen kunnen worden. Naast het helpen bij de voorbereiding op een baan, is 3D-printen een zeer nuttig leermiddel dat de creativiteit stimuleert.
Maar hoe kunnen docenten op alle niveaus aan de slag met 3D-printen in de klas? In deze blog behandelen we waarom klaslokalen 3D-printen nodig hebben en hoe je 3D-printen in de klas kunt integreren.
Voordelen van 3D-printen in de klas
Het is belangrijk dat klaslokalen worden gemoderniseerd. Dit betekent dat leerlingen moeten worden uitgerust met basismiddelen zoals moderne laptops en audiovisuele hulpmiddelen zoals projectoren en smartboards. In plaats van technologie uit het klaslokaal te weren, moeten leerkrachten leerlingen in staat stellen te leren met deze nieuwe technologie. Zo klinken 3D-printers misschien niet fundamenteel, maar ze hebben zich bewezen als essentiële hulpmiddelen.
3D-printers hebben onlangs veel belangstelling gewekt voor onderwijsdoeleinden. Volgens een Department for Education-rapport "hebben 3D-printers een aanzienlijk potentieel als leermiddel en kunnen ze een positieve invloed hebben op de inzet en het leerproces van leerlingen".
3D-printen maakt leren actief, geeft studenten praktische ervaring en brengt hun CAD-projecten tot leven. Naast het lezen van boeken en het maken van aantekeningen bij colleges, kunnen studenten academische concepten toepassen op 3D-printen, waardoor ze de informatie beter kunnen opnemen. Dit is bijzonder nuttig voor ervaringsgerichte leerlingen. In anatomielessen kunnen studenten bijvoorbeeld botten en organen printen om het menselijk lichaam beter te begrijpen. Door 3D-printen verwerven studenten ook analytische vaardigheden - ze interpreteren de grootte, vorm, beweging en relaties tussen objecten.
Bovendien ondersteunt 3D-printen het begrip van de echte wereld. Door al doende te leren, kunnen leerlingen zien welke impact hun 3D-geprinte onderdelen in de echte wereld kunnen hebben. Leerkrachten spelen een belangrijke rol om leerlingen te helpen begrijpen welke impact 3D-printen heeft op het dagelijks leven.
3D-printen in de klas kent toepassingen die verder gaan dan alleen voor de exacte vakken (zoals wetenschap, techniek, wiskunde). 3D-printers zijn creatieve instrumenten die de verbeelding verruimen. Er zijn vrijwel geen grenzen aan wat leerlingen kunnen printen. Leerlingen zonder CAD-vaardigheden kunnen 3D-objecten maken in VR en ze vervolgens printen.
Steeds meer bedrijven starten met innoveren door middel van 3D printing. Zodra je op zoek gaat naar een 3D printer is het mogelijk dat je de keuze moet maken tussen een filament printer en een resin printer, maar welke 3D printer is geschikt voor jouw toepassing? Met meer dan 8 jaar ervaring in 3D printing delen wij graag onze kennis, inzichten en advies in dit verschil, zodat jij de juiste keuze kunt maken tussen een filament printer of een resin printer.
Wat is een filament printer?
Een 3D printer die een filament gebruikt voor het printen van een 3D onderdeel wordt ook wel een Fused Deposition Modeling (FDM) of Fused Filament Fabrication (FFF) printer genoemd. Dit is één van de meest gebruikte vormen van 3D printen op consumentenniveau, maar ook voor bedrijven. Een filament printer bouwt onderdelen door thermoplastische filamenten te smelten en bouwt een onderdeel laagje voor laagje op. Een filament printer werkt met verschillende thermoplasten, waaronder PLA, ABS of CPE. Het is zeer geschikt voor eenvoudige proof-of-concept-modellen of het snel vervaardigen van eenvoudige, grotere prototypes.
De voor- en nadelen van een filament printer
Een filament printer wordt veelal gebruikt door organisaties uit verschillende branches. Hieronder zetten wij alvast de voor- en nadelen van een filament printer op een rij.
De voordelen van een filament printer
- Eenvoudig in gebruik
- Stuk goedkoper dan een resin printer of een metaalprinter
- Keuze in verschillende materialen en kleuren
- Grotere prototypes produceren
De nadelen van een filament printer
- Een filament printer is niet geschikt voor het 3D printen van kleinere onderdelen
- Niet geschikt als details in het onderdeel zeer belangrijk zijn
- Vereist nabewerking
- Het printen met een filament printer kost meer tijd dan een andere 3D printer
Ben je op zoek naar een hoge resolutie 3D-printer? "Resolutie" is een vaak besproken maar zelden begrepen waarde in de wereld van 3D-printen en Additive Manufacturing. Hoe beïnvloedt de XY- en Z-resolutie de kwaliteit van jouw 3D-prints? Wat is de minimale feature size en welke laagdikte moet je kiezen? In deze uitgebreide blog leer je hoe de resolutie van een 3D-printer jouw 3D-prints beïnvloedt, en hoe deze verschilt tussen SLA-, FDM- en DLP-printers.
De resolutie-strijd van bedrijven
Technologie is al tientallen jaren in een resolutieoorlog verwikkeld. Televisies hebben onlangs het aantal pixels verviervoudigd van HD naar 4K en zullen dat binnenkort weer doen met 8K. Mobiele telefoons, tablets en alles wat een scherm heeft, zal de resolutie als eerste op het specificatieblad zetten, op voorwaarde dat het iets is om over te op te scheppen. Maar dit is niets nieuws. Resolutieoorlogen worden al gevoerd sinds digitale technologie populair werd. De grafische industrie was één van de eerste slagvelden.
Wie er in de jaren 80 en 90 bij was, herinnert zich vast dat Canon, Brother, HP, Epson en Lexmark (en anderen) de strijd aangingen over afdruksnelheid en resolutie. Wat begon met 100x100 dots per inch (DPI) escaleerde al snel naar 300x300, toen 600x600 en uiteindelijk naar de huidige industriestandaard van 1200x1200 DPI. Destijds was de betekenis van deze waarden duidelijk te begrijpen; zelfs de eenheden waren volkomen logisch. Helaas wordt het ingewikkelder wanneer je een andere dimensie toevoegt aan printen.
De 3D-printresolutie
Het detailniveau van een print wordt beïnvloed door de resolutie van de 3D-printer in alle drie de dimensies.
Bij 3D-printen en Additive Manufacturing zijn er drie dimensies waarmee rekening moet worden gehouden: de twee vlakke 2D-dimensies (X en Y) en de Z-dimensie die het 3D-printen mogelijk maakt. Aangezien de vlakke en de Z-dimensie doorgaans via zeer verschillende mechanismen worden aangestuurd, zullen hun resoluties verschillend zijn en moeten zij afzonderlijk worden behandeld. Bijgevolg is er veel verwarring over wat de term "3D-printresolutie" betekent en welk niveau van printkwaliteit je mag verwachten.
Vergelijk verschillende 3D-printprocessen en de resolutie
De hoge resolutie SLA-3D-printers van Formlabs hebben een hoge Z-as resolutie en een lage minimale feature size op het XY-vlak, waardoor ze fijne details kunnen produceren.
Wat geeft een 3D-printer zijn hoge resolutie? Er is geen eenduidig antwoord. Aangezien 3D-printers onderdelen in 3 dimensies produceren, moet je rekening houden met minstens twee getallen: de minimale feature size van het XY-vlak en de Z-as resolutie (laagdikte of laaghoogte). De Z-as resolutie is gemakkelijk te bepalen en wordt daarom veel genoemd, ook al heeft zij minder te maken met de printkwaliteit en oppervlakteafwerking. De belangrijkere XY-resolutie (minimale feature size) wordt gemeten met microscopische beeldvormingstechnieken en staat daarom niet altijd in de data sheets.
In de praktijk betekent dit dat je een 3D-printer moet kiezen die in beide categorieën goed presteert (in alle 3 dimensies).
SLA- vs. FDM 3D-printen
Er is veel veranderd sinds de eerste desktop 3D-printers beschikbaar waren voor het publiek. Tegenwoordig concurreren stereolithografie (SLA) 3D-printer zoals de Form 3, om dezelfde desktop-plekken als FDM-3D-printers. Eén van de belangrijkste voordelen van op hars gebaseerde SLA-3D-printers ten opzichte van hun op plastic gebaseerde soortgenoten is de printkwaliteit: SLA-3D-printers produceren aanzienlijk gladdere en gedetailleerdere prints. Hoewel met SLA-printers bovendien aanzienlijk dunnere laagdiktes bereikt worden, ligt de reden voor de verbeterde printkwaliteit in hun veel hogere XY-resolutie.
SLA-3D-printers (rechts) bieden een hogere resolutie en kunnen aanzienlijk gladdere en gedetailleerdere prints produceren dan FDM-3D-printers (links).
Anders dan bij FDM-3D-printers wordt de minimale feature size in het XY-vlak bij SLA-3D-printers niet beperkt door de stromingsdynamiek van gesmolten kunststof, maar door optiek en radicale polymerisatiekinetiek. Hoewel de wiskunde ingewikkeld is (en buiten de scope van deze blog valt), komt het hier op neer: elementen op SLA-prints kunnen ongeveer even klein zijn als de diameter van hun laserspots. En laserspots kunnen heel klein zijn, vooral vergeleken met de nozzle-afmetingen van de extruders van FDM-printers.
Laser SLA- vs. DLP-3D-printers
Resin 3D-printers zoals SLA-, LFS- en DLP-technologieën bieden de hoogste resoluties van alle 3D-printprocessen die als desktop beschikbaar zijn. De basiseenheden van deze processen zijn verschillende vormen, waardoor het moeilijk is de verschillende machines alleen op basis van numerieke specificaties te vergelijken.
DLP-3D-printers hebben een vaste matrix van pixels ten opzichte van de build area. Lasergebaseerde SLA- en LFS-3D-printers daarentegen kunnen de laserstraal op elke XY-coördinaat richten. Dit betekent dat lasergebaseerde machines, mits de optiek van hoge kwaliteit is, het oppervlak van een onderdeel nauwkeuriger kunnen reproduceren. Zelfs als de laserspot groter is dan de DLP-pixelgrootte.
Welk resin 3D-printproces je ook kiest, professionele resin 3D-printers moeten in staat zijn om de fijnste details van jouw creaties vast te leggen, van fotorealistische modellen tot ingewikkelde sieraden.
Vital Auto, gevestigd in het hart van de Britse auto-industrie, is een industriële ontwerpstudio met veel expertise op het gebied van auto-ontwerp. Tot de gerenommeerde klantenkring van het bedrijf behoren vele grote autofabrikanten, waaronder Volvo, Nissan, Lotus, McLaren, Geely en TATA.
"Klanten komen meestal naar ons toe om te proberen de grenzen te verleggen van wat mogelijk is met de beschikbare technologie", aldus Shay Moradi, Vitals VP of Innovation & Experiential Technology. Wanneer fabrikanten geen tijd hebben om zelf te experimenteren, vertrouwen ze op Vital Auto om ideeën, eerste schetsen, tekeningen of technische specificaties om te zetten in een volledig gerealiseerde fysieke vorm.
In deze blog vertellen wij je meer over Vital Auto die high-fidelity prototypes en conceptauto's creëert. Ontdek hoe snel de onderneming door iteraties werkt met behulp van diverse geavanceerde tools, waaronder een grote reeks Form 3L- en Fuse 1-printers.
Het maken van een conceptauto met een 3D printer
Vital Auto werd opgericht in 2015 toen drie vrienden bij elkaar kwamen, hun baan opzegden en besloten een winkel op te zetten - toepasselijk in een garage. Eén van de eerste opdrachten die het bedrijf aannam was voor het supercar-concept NIO EP9. Dit zette het team meteen op een koers om uiterst realistische, high-fidelity voertuigprototypes te produceren.
Van een papier tot het 3D printen van auto-onderdelen
Afhankelijk van het verzoek van de klant begint het team met een eenvoudige schets op een stuk papier tot een reeds ontworpen voertuig. Ze ontwikkelen auto's vanaf een blanco vel, ontwerpen alle hoofdframes, alle exterieur- en interieurelementen, openingen/sluitingen en interactieve elementen. Met 5 tot 30 mensen die aan één concept werken, kan een doorsnee project 3 tot 12 maanden duren.
In die tijd ondergaat een gemiddelde showcar tot een dozijn ontwerpiteraties. En binnen die iteraties kunnen er nog meer aanpassingen van kleinere onderdelen plaatsvinden totdat het ontwerp voldoet aan de verwachtingen van de klant.
"Het is goed in onze sector om naar virtuele eigenschappen te kijken als middel om een product te evalueren voordat het op de markt komt. Maar ik denk dat er ook altijd een plek zal zijn voor fysiek vervaardigde voorwerpen. Er gaat niets boven de sensatie en het gevoel van een object in je handen houden met het juiste gewicht, met de juiste verhoudingen en de dynamiek van hoe de fysieke omgeving je perceptie van dat fysieke object verandert," aldus Moradi.
"Het merendeel van onze klanten komt bij ons met een nieuw idee, een innovatief idee en iets dat nog nooit eerder is gedaan. De uitdagingen voor ons zijn dus elke dag nieuw en eindeloos", stelt Anthony Barnicott, Design Engineer en verantwoordelijk voor Additive Manufacturing. "Deze uitdagingen kunnen variëren van hoe we een bepaalde hoeveelheid onderdelen in een vereiste tijdspanne kunnen produceren, tot hoe we een product duurzaam kunnen maken, of hoe we een onderdeel kunnen maken dat een bepaald gewicht heeft en toch een bepaalde prestatie neerzet."
Hoewel conventionele showcars normaal gesproken alleen van freesklei worden gemaakt, maakt het team ook gebruik van drie- en vijfassig CNC-frezen, handvormen, kleimodellering en GRP-composieten. Deze traditionele processen zijn echter vaak niet ideaal voor de productie van op maat gemaakte onderdelen die nodig zijn voor eenmalige concepten.
"We gebruiken 3D-printen al vanaf het begin. We wilden het niet alleen in onze productieprocessen introduceren om de kosten te verlagen, maar ook om de klant meer diversiteit te geven in hun ontwerpen en ideeën," zegt Barnicott.
Vandaag beheert Barnicott een hele afdeling voor 3D-printen, inclusief 14 grootformaat FDM-printers, drie Formlabs 3L grootformaat SLA-printers en vijf Fuse 1 SLS-printers.
"Qua capaciteit draaien al die printers 100%, 24/7, zo ongeveer vanaf de eerste dag. We gebruiken deze printers voor al onze concepten en ontwerpen. Meestal gebruiken we de Fuse 1's voor onze productieonderdelen en de Form 3L's voor onze conceptonderdelen," aldus Barnicott.
Complexe ontwerpen produceren uit meerdere materialen met de Form 3L
"Wij gebruiken de Form 3L-machines voor alles met een A-klasse afgewerkt oppervlak. Dus meestal in een auto-omgeving, een interieur waar je onderdelen hebt die niet worden bekleed met leer of Alcantara of een soort stof. De materialen van Formlabs geven ons een mooie, gladde afwerking waarmee onze schilders direct uit de voeten kunnen. Ook kunnen onderdelen rechtstreeks uit de printer in een voertuig toepassen," stelt Barnicott.
"Wat mij het meest interesseert aan de Form 3L-machines is hun veelzijdigheid. Je hebt de mogelijkheid om in minder dan vijf minuten van materiaal te wisselen. De grote variatie in materialen – deze kunnen zacht en flexibel zijn, maar ook hard en stijf - is voor ons onbetaalbaar", aldus Barnicott.
Het team gebruikt de Form 3L's met meerdere materialen voor een groot aantal toepassingen, waaronder:
Luchtroosters
"Een gangbare uitdaging voor ons als bedrijf is dat klanten ons benaderen met een eigen product en dat in hun eigen ontwerp willen verwerken. Zo benaderde een klant ons met een eigen luchtrooster van een ander voertuig die hij in zijn eigen interieur wilde hebben. We gebruikten 3D-scantechnologie om dit onderdeel digitaal te reproduceren en creëerden vervolgens een uitwendige schil. Die produceerden we eerst in het materiaal Draft om het ontwerp te testen en de klant de kans te geven het te verifiëren. Daarna zijn we overgestapt op het materiaal White om een productie klaar onderdeel te produceren."
Schakelpakketten
"Wanneer we werken met ongelooflijk ingewikkelde ontwerpen zoals kleine schakelpakketten, kunnen we meerdere materialen gebruiken om een mechanisch product te maken dat niet alleen goed functioneert, maar ook kan worden gebruikt in een real-world omgeving. Voor deze schakelpakketten hebben we hardere materialen zoals de Tough 2000 voor de bovenkant gecombineerd met de lichtere, kosteneffectievere materialen voor de binnenkant."
Deurafdichtingen
"Doorgaans is de productie van deurafdichtingen voor automobieltoepassingen ongelooflijk duur. Er is gewoon geen andere manier dan extrusiegieten om ze te produceren. Dit brengt niet alleen hoge gereedschapskosten met zich mee, maar ook een lange doorlooptijd. We konden experimenteren met een van Formlabs' nieuwste materialen, de Flexible 80A. Met de Form 3L konden we 's nachts secties van deze deurafdichting printen om verschillende geometrieën te testen. Dit printen ging met een nauwkeurigheid van 50 micron."
Met de Form 3L kan het team in de meeste gevallen binnen 24 uur meerdere iteraties van onderdelen produceren. Uiteindelijk kochten ze drie verschillende machines. Zo konden ze tot drie verschillende iteraties van een onderdeel tegelijk produceren, zelfs met drie verschillende materialen. Vervolgens kunnen ze de kostenbesparing doorberekenen aan de klant of meer waarde bieden door meerdere ontwerpopties voor dezelfde prijs te tonen.
"Eén van de voordelen van Additive Manufacturing is de snelheid in de tijd. Maar wat doe je met de vrijgekomen tijd? Wij gebruiken deze om meer mogelijke alternatieven te bedenken of het toevoegen van extra iteratielussen in het proces," aldus Moradi.
"Er zijn veel producten die we zonder onze Form 3L's simpelweg niet zouden kunnen maken. Althans, het zou wellicht lukken met enkele zeer geavanceerde productietechnieken zoals zevenassig CNC-frezen. Maar dit zou wel gepaard gaan met enorme compromissen", zegt Barnicott.
Wat betekenen Notched Izod van 14 J/m, post-cured en ASTM D 256-10 eigenlijk? Wat is het verschil tussen sterkte en modulus? Hoe houden ze verband met gewone materialen die we dagelijks tegenkomen, en waarom is dat voor jou van belang?
Materiaaleigenschappen zoals chemische, optische, mechanische, thermische of elektrische eigenschappen geven aan hoe een bepaald materiaal zich onder bepaalde omstandigheden gedraagt. Gekwantificeerd kunnen deze eigenschappen je helpen de voordelen van het ene materiaal tegenover het andere te beoordelen voor een specifieke use case.
In deze blog beschrijven we de meest gebruikte mechanische en thermische eigenschappen en hun belang voor specifieke toepassingen. Ook beschrijven we hoe 3D-geprinte materialen zich verhouden tot kunststoffen die met conventionele methoden zijn vervaardigd. Zo helpen we je om de juiste materiaalkeuze te maken voor jouw 3D-printer.
Voornaamste mechanische en thermische eigenschappen van 3D onderdelen
Laten we beginnen bij het begin: de verschillende eigenschappen en waarom deze zo belangrijk zijn.
- Treksterkte: Weerstand van een materiaal tegen breken onder spanning. Dit is de fundamentele eigenschap die de uiteindelijke sterkte van een onderdeel aangeeft. Een hoge treksterkte is belangrijk voor structurele, dragende, mechanische of statische onderdelen.
- Elasticiteitsmodulus: Weerstand van een materiaal tegen uitrekken onder spanning (stijfheid). Dit is een oede indicator voor ofwel de stijfheid (hoge modulus) ofwel de flexibiliteit (lage modulus) van een materiaal.
- Rek: Weerstand van een materiaal tegen breken bij uitrekken. Dit helpt je om flexibele materialen te vergelijken op basis van hoeveel ze kunnen uitrekken. Geeft ook aan of een materiaal eerst zal vervormen of plotseling zal breken.
- Buigsterkte: Weerstand van een materiaal tegen breken bij buigen. Dit is vergelijkbaar met treksterkte, maar toont de sterkte in buigmodus. Tevens een goede indicator of een materiaal isotroop (homogeen) is.
- Buigmodulus: Weerstand van een materiaal tegen buigen onder belasting. Dit geeft een goede indicator voor ofwel de stijfheid (hoge modulus) ofwel de flexibiliteit (lage modulus) van een materiaal.
- Kerfslagwaarde: Het vermogen van een materiaal om schokken en impactenergie te absorberen zonder te breken. Dit geeft de stevigheid aan, helpt je te bepalen of een onderdeel zal standhouden als het op de grond valt of tegen een ander voorwerp botst.
- Hardheid (Shore): Weerstand van een materiaal tegen vervorming. Dit helpt je om de juiste "zachtheid" te bepalen voor rubber en elastomeren voor bepaalde toepassingen.
- Compressie: Permanente vervorming die overblijft nadat materiaal is samengeperst. Dit is belangrijk voor elastische toepassingen, geeft aan of een materiaal snel terugveert in zijn oorspronkelijke vorm.
- Scheursterkte: Weerstand van een materiaal tegen het ontstaan van sneden onder spanning. Dit is belangrijk voor flexibele materialen, zoals rubber of textiel. Toont de weerstand tegen scheuren.
- Waterabsorptie: Hoeveelheid geabsorbeerd water onder bepaalde omstandigheden. Dit is vooral belangrijk tijdens de verwerking van de grondstof. Een hoge waterabsorptie of vochtigheid kan leiden tot slechte materiaaleigenschappen in thermoplasten.
- Warmtevormvastheidstemperatuur: Temperatuur waarbij een sample vervormt onder een bepaalde belasting. Dit geeft aan of een materiaal geschikt is voor toepassingen bij hoge temperaturen.
- Vicat-verwekingstemperatuur: Temperatuur waarbij het materiaal merkbaar zacht wordt. Dit wordt gebruikt voor materialen die geen duidelijk smeltpunt hebben. Voor toepassingen bij hoge temperaturen helpt het de bovengrens van de temperatuur voor continu gebruik te bepalen.
- Thermische expansie: De neiging van een materiaal om uit te zetten (of te krimpen) als reactie op een temperatuursverandering. Dit is belangrijk voor toepassingen waarbij een vormverandering als reactie op de temperatuur onaanvaardbaar of wenselijk is.
Materiaaleigenschappen worden het meest betrouwbaar gemeten met gestandaardiseerde testmethoden. Veel van die methoden zijn gedocumenteerd door hun respectieve user communities en worden gepubliceerd door ASTM International. Natuurlijk zijn de exacte meetwaarden voor jouw onderdelen afhankelijk van het ontwerp. Door gestandaardiseerde tests te vergelijken, krijg je echter een idee van hoe jouw onderdeel zich zal gedragen als het volgens verschillende methoden uit verschillende materialen wordt vervaardigd. De kans is groot dat je deze metrieken en normen tegenkomt op datasheets van materialen.
Nu we een duidelijk inzicht hebben in de basisprincipes, gaan we dieper in op elke materiaaleigenschap. We behandelen benchmarks voor materialen die zijn gemaakt met conventionele productiemethoden, maar ook met gangbare 3D-printtechnologieën zoals Fused Deposition Modeling (FDM), Stereolithografie (SLA), Selective Laser Sintering (SLS) en PolyJet.
De treksterkte van een 3D onderdeel
Eén van de belangrijkste materiaaleigenschappen is de treksterkte, de weerstand van een materiaal tegen breken onder spanning. Het is een van de eerste materiaaleigenschappen waar ingenieurs naar kijken en die bovenaan de meeste materiaaldatasheets staat. In combinatie met voldoende vervormbaarheid geeft de treksterkte ook de stevigheid van een materiaal aan. Sommige materialen breken zeer scherp in een brosse breuk, terwijl meer taaie materialen, zoals de meeste kunststoffen en metalen, enige vervorming ondergaan. Om dit gedrag duidelijk te begrijpen, worden gegevens over de treksterkte gewoonlijk aangevuld met een spanning-rekdiagram.
Materialen met een hoge treksterkte worden doorgaans aangetroffen in structurele, mechanische of statische onderdelen waar een breuk onaanvaardbaar is. Denk bijvoorbeeld aan de bouw, de auto-industrie en de luchtvaart, maar ook in draden, touwen, kogelvrije vesten en meer. Tegenwoordig is 3D-printen zo ver gevorderd dat het dezelfde of zelfs een hogere treksterkte kan leveren dan traditionele spuitgietkunststoffen zoals polypropyleen en ABS.
De elasticiteitsmodulus van 3D onderdelen
De elasticiteitsmodulus van Young is een maat voor de stijfheid van een materiaal onder trekbelasting. Hoe hoger de elasticiteitsmodulus, hoe stijver het materiaal. Aan de bovenkant van de schaal kwantificeert de elasticiteitsmodulus de vormvastheid van een materiaal onder belasting. Dit is één van de eerste eigenschappen die je moet onderzoeken bij het selecteren van materialen voor dragende mechanische en structurele onderdelen die onder belasting binnen hun geometrische specificaties moeten blijven.
Een lage elasticiteitsmodulus wijst daarentegen op een elastisch materiaal. Aan de onderkant van de schaal kun je met de elasticiteitsmodulus dus inzicht krijgen in de elasticiteit van een zacht en flexibel materiaal.
De rek van een 3D onderdeel
De mate waarin een materiaal uitrekt op het moment dat het breekt, wordt rek genoemd. Gedefinieerd als de verhouding van de verlenging tot de aanvankelijke, onbelaste lengte, drukt zij het vermogen van een materiaal uit om vormveranderingen te weerstaan zonder scheurvorming. Stijve materialen, zoals brosse-harde kunststoffen, hebben doorgaans een geringe rek bij breuk. Sommige zachte, elastische materialen daarentegen kunnen meerdere malen hun eigen lengte uitrekken alvorens ze breken.
Bij de keuze van een flexibel materiaal voor een specifieke toepassing geeft rek aan hoeveel het kan uitrekken. Rek is ook belangrijk in de bouw en architectuur, waar structuren merkbaar moeten vervormen in plaats van onmiddellijk in te storten. Als de rek kan worden afgeleid uit de treksterkte en de trekmodulus van een materiaal, is het dus een deels overbodige maatstaf.
De buigsterkte van een 3D onderdeel
Net als de treksterkte beschrijft de buigsterkte de weerstand van een materiaal tegen breken onder belasting. Het verschil ligt in het soort belasting. Bij buigsterkte gaat het om een buigbelasting, waardoor zowel de druk- als de treksterkte van een materiaal wordt weergegeven.
Voor de meeste kunststoffen liggen buigsterkte en treksterkte dicht bij elkaar. Als een materiaal isotroop (homogeen) is, is de buigsterkte gelijk aan de treksterkte. Door de sterke chemische bindingen in de 3D-prints zijn SLA-onderdelen isotroop. Dit is een groot voordeel ten opzichte van andere 3D-printtechnologieën, omdat de onderdelen ongeacht de oriëntatie een vergelijkbare sterkte hebben.
De buigmodulus van een 3D onderdeel
De buigmodulus is een maat voor de stijfheid van een materiaal in buigrichting. Een hoge buigmodulus wijst op een stijver materiaal. Elastische materialen daarentegen hebben een lagere buigmodulus. Net als trek- en buigsterkte zijn trek- en buigmodulus nauw verwant en verschillen ze doorgaans niet veel van elkaar.
De buigmodulus is een belangrijke metriek voor toepassingen als stalen veren - met name bladveren - en steunbalken of constructiedelen.
De kerfslagwaarde van een onderdeel
Materialen kunnen anders reageren op statische belastingen dan op abrupte schokken. Het vermogen om deze abrupte energie te absorberen tijdens plastische vervorming is de taaiheid van een materiaal. Impactproeven, gedefinieerd als de hoeveelheid energie die een materiaal kan absorberen bij een plotselinge botsing of schok zonder te breken, zijn een goede indicator voor taaiheid. Broze materialen hebben een lage taaiheid als gevolg van de geringe hoeveelheid plastische vervorming die zij kunnen verdragen. Over het algemeen neemt bij lagere temperaturen de kerfslagenergie die een materiaal kan absorberen ook af.
Kerfslagvastheid is een belangrijke factor in vele toepassingen, van behuizingen tot schilden en veiligheidsbrillen. De Izod-slagproef en de Charpy-kerfslagproef zijn twee gangbare proeven voor slagvastheid die alleen verschillen in de manier waarop ze worden gemeten, waarbij de eerste de ASTM-norm is.
De hardheid (Shore) van een 3D onderdeel
Hardheid wordt gedefinieerd als de weerstand van een materiaal tegen permanente vormverandering wanneer een drukkracht wordt uitgeoefend. In de praktijk is hardheid synoniem met krasbestendigheid en weerstand tegen indrukken en elastische vervorming. Contra-intuïtief gezien sluiten hardheid en taaiheid elkaar uit. Harde materialen zijn van nature bros. Taaiheid daarentegen vereist dat een materiaal een zekere ductiliteit (vervormbaarheid) bezit.
Hoewel een lage hardheid over het algemeen wijst op een zacht materiaal, wordt de bovenstaande definitie van hardheid steeds minder praktisch naarmate het geteste materiaal zachter is. Dit is waar de Shore-durometer (of Shore-hardheid) in beeld komt - een testmethode en definitie voor het meten van de hardheid (of zachtheid) van zachte, flexibele en elastische materialen zoals rubber, elastomeren en sommige polymeren.
In de praktijk wordt de Shore-durometer vaak gebruikt om geschikte materialen te identificeren voor zacht aanvoelende oppervlakken, zoals een handgreep of het juiste rubber voor een specifieke pakking. De durometer is ook een belangrijke maatstaf voor rollen en massieve banden. Een hoge Shore-hardheid wijst op een harder en minder flexibel materiaal. Een lagere waarde daarentegen duidt op een zachter materiaal.
Als een gegevensblad geen waarde voor de hardheid vermeldt, kan een lage trekmodulus ook een goede indicator zijn voor een elastisch en zacht materiaal. De ASTM-testnorm voorziet in een totaal van 12 schalen, waarbij de A-schaal de meest gebruikelijke is voor zachtere kunststoffen en de D-schaal voor hardere.
De compressieset van een 3D onderdeel
Compressieset wordt gewoonlijk gebruikt om de permanente vervorming te beschrijven die in een zacht materiaal, zoals een elastomeer, overblijft nadat een drukkracht is weggenomen.
Materialen met een hoge compressieset zijn ongeschikt voor toepassingen waar van een onderdeel wordt verwacht dat het snel in zijn oorspronkelijke vorm terugspringt nadat een drukkracht is verwijderd, zoals veren. Voor dempers of pakkingen kan een hoge compressieset aanvaardbaar of gewenst zijn.
De scheursterkte van een 3D onderdeel
De scheursterkte beschrijft de weerstand van een materiaal tegen scheuren, vooral tegen het ontstaan van sneden en de verspreiding daarvan door het materiaal onder belasting. Materialen met een lage scheurweerstand zijn doorgaans slecht bestand tegen slijtage en zullen bij beschadiging snel bezwijken.
De scheursterkte is een belangrijke factor bij de keuze van flexibele materialen zoals rubber of textiel voor toepassingen met hoge spanning. Materialen die worden gebruikt voor gespannen membranen, trommels of zeildoek, elastieken en bungees moeten bestand zijn tegen scheuren, zelfs na een eerste beschadiging, Deze materialen vereisen daarom een hoge scheursterkte.
De waterabsorptie van 3D onderdelen
Kunststoffen absorberen een bepaalde hoeveelheid water uit vochtige lucht of bij onderdompeling in water. Hoewel sommige kunststoffen hygroscopischer zijn dan andere, is deze minuscule waterabsorptie voor de uiteindelijke kunststofproducten zelden van belang. Het speelt echter wel een belangrijke rol bij de verwerking van de grondstoffen en bij de hittebestendigheid van kunststof onderdelen.
Bij verhitting boven een bepaalde temperatuurgrens - meestal rond 150 - 160°C - ondergaan veel thermoplasten in aanwezigheid van vocht een chemische reactie genaamd hydrolyse. Hierbij worden lange molecuulketens gesplitst in kortere en het materiaal wordt zwakker. Als een thermoplastische grondstof met een hoge waterabsorptie vóór het 3D-printen of spuitgieten aan vochtigheid wordt blootgesteld, treedt tijdens het proces hydrolyse op. Dit leidt tot slechte materiaaleigenschappen van het uiteindelijke onderdeel. Daarom moeten thermoplastische grondstoffen met een hoge waterabsorptie in een droge omgeving worden opgeslagen.
Terwijl spuitgietkunststoffen (ABS, nylon, polypropyleen) thermoplasten zijn, zijn SLA fotopolymeren resins thermohardende materialen. Deze worden met een lichtbron uitgehard in plaats van in vorm gesmolten, en blijven na uitharding in een permanente vaste toestand. Daardoor zijn ze niet gevoelig voor de negatieve effecten van hydrolyse.
De warmtevervormingstemperatuur (HDT) van een 3D onderdeel
Materiaaleigenschappen, met name trek- en buigmoduli, zijn gebonden aan de gestandaardiseerde omgevingsomstandigheden waaronder hun testresultaten zijn vastgelegd. Verschillende omgevingsomstandigheden, zoals verschillende omgevingstemperaturen, kunnen leiden tot een aanzienlijke verandering van de prestaties van een materiaal onder belasting. De warmtevervormingstemperatuur (HDT) geeft de temperatuur aan waarbij een materiaal onder een bepaalde belasting begint te vervormen. Een hoge HDT is wenselijk voor toepassingen bij hoge temperaturen, zoals behuizingen en bevestigingen voor verwarmingselementen. Een hoge HDT is ook geschikt voor onderdelen die in contact komen met hete vloeistoffen of gassen, zoals gereedschappen voor spuitgietmatrijzen, verbindingsstukken voor vloeistoffen, kleppen en spuitmonden.
Het Vicat-verwekingspunt van een 3D onderdeel
In tegenstelling tot andere materialen hebben kunststoffen geen scherp smeltpunt. Het Vicat-verwekingspunt fungeert als een alternatieve definitie van het punt waarop een materiaal begint te vloeien en deze leemte opvult voor kunststoffen en thermoplasten. Net als het HDT geeft het Vicat-verwekingspunt de verandering van de mechanische eigenschappen van een materiaal onder invloed van warmte weer. Het markeert een temperatuurpunt waar een gestandaardiseerde naald een testmonster met een bepaalde lengte en een bepaalde belasting indrukt.
Het wordt meestal gebruikt om de bovenste temperatuurgrens te bepalen voor continu gebruik van een materiaal in een toepassing bij een verhoogde bedrijfstemperatuur die, als vuistregel, 15 °C onder het Vicat-weekpunt moet liggen.
De thermische uitzettingscoëfficiënt van een 3D onderdeel
Materialen hebben de neiging te krimpen, uit te zetten of anderszins van vorm te veranderen onder invloed van veranderingen in temperatuur. Dit verschijnsel wordt gebruikt in thermische actuatoren, thermische sensoren en zelfs kunstmatige spieren. In de meeste gevallen is het echter een ongewenst neveneffect dat met veel moeite moet worden ondervangen. De thermische uitzettingscoëfficiënt is een nuttige indicator om te voorspellen en kwantificeren hoe een materiaal van vorm verandert als reactie op temperatuurveranderingen. Een positieve thermische uitzettingscoëfficiënt geeft aan dat het materiaal uitzet bij toenemende temperatuur. Een negatieve coëfficiënt wijst daarentegen op krimp.
Bij het werken met thermoplasten, of het nu gaat om spuitgieten of 3D-printen, moet rekening worden gehouden met de thermische uitzetting van het materiaal om de gewenste vorm te verkrijgen nadat het onderdeel is afgekoeld. Om thermische verschijnselen zoals hoepelkrimp, omkrullen en kromtrekken te voorkomen, die een belangrijke beperking vormen bij het bereiken van geometrische precisie via 3D printtechnologieën zoals SLS en FDM, is het raadzaam om bij de materiaalkeuze rekening te houden met de thermische uitzettingscoëfficiënt.
Thermohardende 3D-printtechnologieën, zoals SLA, hebben over het algemeen geen last van thermische vervormingen. Hierdoor zijn ze een uitstekende keuze voor onderdelen die de hoogste nauwkeurigheid en vormgetrouwheid vereisen.
In de afgelopen tien jaar heeft de toepassing van additive manufacturing elke industrie bereikt. Niet langer meer voornamelijk het domein van hobbyisten, zijn krachtige, betrouwbare 3D-printers uitgegroeid tot essentiële hulpmiddelen voor bedrijven. 3D-printen kan de productiesnelheid verhogen, de kosten verlagen, alsook snelle prototypes en innovatieve producten en ontwerpen mogelijk maken. Maar hoe verandert het landschap van 3D-printen? Welke nieuwe toepassingen winnen aan populariteit? In dit uitgebreide blogartikel vertellen we hier alles over.
De populariteit van 3D-printen is toegenomen nu het zich heeft gevestigd als een toegankelijke aanvulling op conventionele productie. Dit rapport is een momentopname van de huidige markt voor additive manufacturing en een diepgaand onderzoek naar traditionele en nieuwere toepassingen van additive manufacturing. Het onderzoekt hoe consumenten additive manufacturing gebruiken, in welke soorten technologieën zij investeren en wat zij verwachten in de komende jaren.
3D printen bevindt zich niet meer in de early adaptor-fase
3D-printen is de early adopter-fase voorbij, maar vertoont nog steeds tekenen van robuuste groei en uitbreiding naar nieuwe industrieën en toepassingen.
Om beter te begrijpen hoe het gebruik van 3D-printing zich ontwikkelt, wordt in dit verslag gekeken naar twee belangrijke gebruikersgroepen: de early adopters, die meer dan twee jaar geleden zijn begonnen met additive manufacturing, en de recent adopters, die de afgelopen twee jaar in de technologie hebben geïnvesteerd.
Uit het rapport blijkt dat het aantal nieuwe 3D-printtoepassingen binnen de recent adoptersgroep aanzienlijk is toegenomen. Terwijl rapid prototyping en het maken van modellen populaire use-cases blijven, is een groot aantal bedrijven begonnen met het inzetten van 3D-printen voor kleine series aangepaste productie en het maken van onderdelen voor eindgebruik. Bij recente adopters gebruikt 48% van de bedrijven 3D-printing voor de productie van kleine aantallen op maat gemaakte onderdelen. Bovendien is het frequente gebruik van 3D-printen voor het maken van onderdelen voor eindgebruik sterk gericht op recent adopters: 63% van de recent adopters maakt vaak of altijd gebruik van 3D-printen voor onderdelen voor eindgebruik, tegenover slechts 33% van de early adopters. Het gebruik van onderdelen voor eindgebruik is sterk gericht op nieuwe recent adopters: 63% van de recent adopters gebruikt vaak of altijd 3DP voor onderdelen voor eindgebruik, vergeleken met slechts 33% van de early adopters.
Deze verschuiving onder de recent adopters vertegenwoordigt het toenemende gebruik van 3D-printen om beter in te spelen op de behoeften van de klant en om producten en workflows aan te passen aan veranderende markten. Het toont aan dat additive manufacturing bedrijven zal blijven stimuleren en beïnvloeden bij het stroomlijnen en moderniseren van hun workflows.
De bevindingen in dit rapport zijn gebaseerd op meer dan 400 unieke antwoorden uit een onderzoek van Formlabs, van zowel huidige gebruikers als niet-gebruikers van 3D-printen. 72% van de respondenten maakt momenteel gebruik van 3D-printen, terwijl 28% van de respondenten dat niet doet.
Het onderzoekspanel bestaat uit:
Beroep:
- Productie-ingenieur: 5,6%
- Directeur Innovatie: 6,8%
- Design Engineer / Lead Design Engineer: 20,1%
- Bedrijfseigenaar: 14,1%
- Engineering Manager: 12,1%
- Ontwerper / Senior Ontwerper: 9,6%
- Mechanisch ingenieur: 10,7%
- 3D-printing afdelingshoofd: 11,6%
- Anders: 9,3%
Locatie:
- Noord-Amerika: 60.9%
- EMEA + Azië :39.1%
De Additive Manufacturing-industrie in 2022
Door de dalende kosten van apparatuur is in-house 3D-printen steeds gebruikelijker geworden. Meer dan zeven op de tien (72%) deelnemers aan het onderzoek gaven aan dat hun bedrijf momenteel 3D-printers gebruikt, waarbij de meerderheid in-house print (55%) in vergelijking met het uitbesteden van 3D-printen (17%). Deze trend sluit aan bij de recente opkomst van professionele desktopprinters die nu voor een fractie van de prijs dezelfde kwaliteit bieden als industriële machines uit het verleden.
"3D-printen is als de echte undo-knop, waardoor ik moediger kan zijn in mijn ontwerpproces." Kat Ermant - Hoofd prototype-technicus, Peloton
"In het museumvak heeft 3D-printen ons denken verruimd en ons in staat gesteld de lat hoger te leggen." Mei-An Tsu - Conservator objecten, Museum voor Schone Kunsten
Er zijn twee voornaamste manieren waarop een bedrijf baat kan hebben bij additive manufacturing. Ze kunnen:
- Investeren in intern 3D-printen.
Interne teams voorzien van hun eigen 3D-printers brengt een investering met zich mee, maar verlaagt de kosten per print aanzienlijk in vergelijking met uitbesteding. Het maakt ook verzending overbodig, zodat prints direct na voltooiing kunnen worden gebruikt. In-house 3D beschermt het bedrijf tegen problemen in de supply chain. Dit houdt in dat de productie niet wordt onderbroken door vertragingen in de verzending.
- Gebruikmaken van 3D-printdiensten.
Bedrijven kunnen hun digitale bestanden naar een servicebureau sturen, dat vervolgens de onderdelen 3D-print en terugstuurt. Deze methode heeft geen investeringskosten vooraf, maar terugkerende printkosten zijn duur op de lange termijn. Uitbesteding leidt ook tot lange doorlooptijden, waarbij bedrijven een week tot een maand moeten wachten om hun prints te ontvangen.
Deze getallen worden naar boven bijgesteld door bedrijven in Europa, het Midden-Oosten en Afrika (EMEA). EMEA-bedrijven lopen voor op hun Noord-Amerikaanse tegenhangers: 88% van de respondenten zegt te investeren in in-house of uitbesteed 3D-printen, vergeleken met 64% in Noord-Amerika.
Welke 3D-printprocessen zijn het populairst?
Fused deposition modeling (FDM), ook bekend als Fused Filament Fabrication (FFF), is de meest gebruikte vorm van 3D-printen op consumentenniveau, gevoed door de opkomst van hobbyistische 3D-printers. Mede door de lage prijs is FDM de meest gebruikte 3D-printtechnologie voor onze respondenten. Maar nu gebruikers additive manufacturing beginnen toe te passen voor de productie van onderdelen voor eindgebruik, is het belang van Selective Laser Sintering (SLS) zichtbaar geworden. Met het oog op toekomstige investeringen zegt een groot deel van de respondenten dat SLS het belangrijkste is in termen van verwachte impact op hun bedrijf (46%), meer dan de verwachte impact van SLA (36%). Dit ondanks het feit dat slechts 34% van de gebruikers momenteel SLS gebruikt, en dit is een goed teken voor toekomstige investeringen in SLS-technologie.
De toenemende investeringen in andere technologieën dan FDM worden duidelijk wanneer men de early adopters vergelijkt met de new adopters. Binnen het groep nieuwe gebruikers blijft FDM de meest gebruikte technologie, maar er zijn opvallende verschuivingen naar investeringen in andere technologieën. Een reden hiervoor is de dalende kostprijs van de toegang tot sommige van deze nieuwe technologieën, waaronder SLA- en SLS-3D-printen.
Een overzicht van de momenteel gebruikte 3D-printtechnologieën, waarin recent en early adopters worden vergeleken.
- Stereolithografie (SLA): 56% van de adopters tegenover 46% van de early adopters.
- Selective Laser Sintering (SLS): 44% van de adopters tegenover 27% van de early adopters.
- Fused Deposition Modeling (FDM): 74% van de adopters tegenover 78% van de early adopters.
Medewerkers voor Additive Manufactering-functies
Gezien het tempo waarin intern 3D-printen is ingevoerd en de meeste bedrijven een verdere uitbreiding van 3D-printtoepassingen verwachten, is het geen verrassing dat meer dan de helft van de respondenten een specifiek aantal medewerkers heeft voor additive manufacturing-functies. Het is mogelijk dat dit de komende jaren veel gebruikelijker zal worden. Veel gebruikers van Formlabs 3D-printers zijn algemene ingenieurs op de werkvloer of individuele ontwerpers die onderdelen printen voor hun eigen producten. Naarmate het aantal 3D- printtechnologieën en hun toepassingen groeit, zal er veel vraag zijn naar gebruikers met specifieke vaardigheden op het gebied van additive manufacturing.
3D-printingapplicaties: een groeiend landschap
De belangrijkste drijfveer achter de early adoption van additive manufacturing door de meeste bedrijven is lange tijd het maken van prototypes en modellen geweest. 3D-ontwerpen tot leven brengen om feedback en iteratie te genereren is een essentiële toepassing voor een groot aantal industrieën. Onze onderzoeksgegevens bevestigen dit, waarbij rapid prototyping (58%) en het maken van modellen en rekwisieten (53%) de meest gebruikte toepassingen zijn.
Deze use cases zullen ongetwijfeld populair blijven, vooral nu er nieuwe materialen worden geïntroduceerd die de grenzen van prototyping verleggen. Meer duurzaamheid, grotere flexibiliteit, biocompatibiliteit en andere eigenschappen van polymeren kunnen ze geschikt maken voor industrie- en toepassingsspecifieke prototyping.
Eén van de belangrijkste trends in de industrie wordt gedreven door recent adopters: productie in kleine series en de inzet van onderdelen voor eindgebruik zijn in populariteit toegenomen. Gebruikers maken gebruik van 3D-printen om niet alleen het productontwerp te controleren, maar ook om producten te maken. De kans dat recent adopters regelmatig onderdelen voor eindgebruik printen is ongeveer twee keer zo groot als bij early adopters.
De voordelen van 3D printing
Bij de beoordeling van de voordelen van specifieke 3D-printtoepassingen werd de mogelijkheid om snel te innoveren het meest genoemd door de respondenten. Andere vaker genoemde voordelen voor alle toepassingen waren speed to market, concurrentievoordeel, voldoen aan de vraag van de klant en geld besparen. De uitbreiding van het aantal toepassingen van 3D-printen ging gepaard met een verruiming van de behoeften en opvattingen van gebruikers over wat de technologie hun bedrijf te bieden heeft. We kunnen concluderen dat er de komende jaren waarschijnlijk meer ruimte is voor voortdurende uitbreiding van additive manufacturing en dat de huidige investeringen niet zijn gestagneerd.
De voordelen van in-house rapid prototyping
In-house rapid prototyping voorziet in veel van deze behoeften, zoals speed to market. Maar gebruikers leren dat ze ook een concurrentievoordeel kunnen behalen door het maken van onderdelen voor eindgebruik in-house uit te voeren, of de speed to market kunnen opvoeren door de productie in-house te realiseren. Van de recent adopters is 60% begonnen met 3D-printen voor snelle tooling (vacuümvormen, thermovormen, spuitgieten, enz.), vergeleken met slechts 30% van de early adopters. Met 3D-printen voor rapid tooling kunnen bedrijven de kloof overbruggen tussen traditionele gereedschappen en puur 3D-printen. Het is een kosteneffectieve en snelle manier om onderdelen in beperkte hoeveelheden te produceren.
Geldbesparing - of kostenbesparing - wordt vooral door recent adopters als een belangrijk voordeel gezien. 78% van de recent adopters noemt kostenbesparing als een belangrijk of zeer belangrijk voordeel van 3D-printen, vergeleken met 47% van de early adopters. Dit kan waarschijnlijk worden toegeschreven aan de dalende kosten van een breed scala aan printtechnologieën.
Nieuwe voordelen van 3D-printing
Als gevolg van culturele veranderingen en de COVID-19-pandemie die in 2020 begon, zijn er nieuwe voordelen van in-house 3D-printen opgedoken. In 2021 vond 65% van de recent adopters het belangrijk of zeer belangrijk om op afstand te starten en te controleren, vergeleken met slechts 32% van de early adopters.
De nieuwere adoptergroep van 3D-printen heeft blijkbaar een beroep gedaan op 3D-printen om hen te helpen tijdens de pandemie: 57% van hen is het er "mee eens" of "sterk mee eens" dat hun interne 3D-printmogelijkheden helpen bij het oplossen van problemen met de supply chain. Naast zorgen over de supply chain volgen recent adopters culturele trends op het gebied van duurzaamheid. 70% van de recent adopters noemt duurzaamheid als belangrijk of zeer belangrijk voordeel van 3DP, vergeleken met 30% van de early adopters.
De Selective Laser Sintering (SLS) 3D-printer, Fuse 1, is pas één jaar op de markt en is sinds de lancering al goed voor bijna de helft van alle verkochte SLS-printers. Door zijn compacte ontwerp, intuïtieve workflow en betaalbare prijs stelt de Fuse 1-printer kleine bedrijven in staat om SLS-printen in huis te halen. Daarnaast stelt het grotere bedrijven in staat om de productie eenvoudig en betaalbaar op te schalen. Op basis van de ervaring van onze deskundige gebruikers hebben we de belangrijkste informatie verzameld voor iedereen die overweegt SLS aan zijn workflow toe te voegen. In dit artikel lees jij alles wat je over de Fuse 1 moet weten.
In dit artikel behandelen we:
- Infrastructuurvereisten voor de Fuse 1 en Fuse Sift
- Tips voor workflow-efficiëntie en productiviteit
- Aanbevelingen voor nabewerking
- Veel voorkomende zorgen over SLS-printen en hoe de Fuse 1 deze aanpakt
Toegankelijkheid van de Formlabs Fuse 1: afmetingen, vermogen, accessoires
Formlabs heeft de Fuse 1 ontwikkeld met het oog op toegankelijkheid. De meeste bedrijven hebben niet veel extra vierkante meters in hun faciliteiten, noch de mogelijkheid om meerdere gespecialiseerde circuits toe te voegen die historisch gezien nodig zijn voor SLS-systemen.
Veel van onze klanten werken vanuit kantoorruimtes in plaats van magazijnen en technische faciliteiten en hebben dus beperkte mogelijkheden om de grootte van hun ruimtes, elektrische circuits en ventilatiesystemen te veranderen. De Fuse 1 biedt een oplossing voor dat dilemma; hij is compact ontworpen, eenvoudig te installeren, veilig en handig in gebruik en vereist minimale reiniging.
Omvang van de Formlabs Fuse 1: levering en installatie
Voor de meeste SLS 3D printers zijn hefbruggen en vorkheftrucks nodig voor de installatie. De Fuse 1 en Fuse Sift kunnen door twee personen worden gedragen (met behulp van een hefband tussen hen in), waardoor kantoorgebouwen, trappen en smalle deuropeningen gemakkelijk te manoeuvreren zijn.
Een klant van Formlabs, PrintParts, heeft 12 Fuse 1-printers en 6 Fuse Sifts ontvangen en geïnstalleerd in hun kantoorruimte in Manhattan, zonder grote hefbruggen te hoeven gebruiken of het ventilatiesysteem van hun locatie te veranderen. De initiële PrintParts-opstelling van Fuse 1-printers
De plaats van opstelling, met één Fuse 1-printer en één Fuse Sift, naast elkaar geplaatst, vereist een ruimte van minstens 310 cm breed en 146 cm diep (vanaf een muur). Een normale plafondhoogte van 2,5 m is prima. De tussenruimte en toegangspunten kunnen veranderen als je jouw machines uitbreidt (als je bijvoorbeeld 4 Fuse 1-printers tegen een muur heeft staan, hoeft er maar 30,5 cm tussen te zitten), maar de belangrijkste regels voor deze SLS printers zijn:
- Fuse 1 afmetingen: diepte(64,5cm) x H(107cm) x B(68,5cm)
- Tussenruimte voor de Fuse 1:
- 20 cm (8in) afstand van elke muur (zij- en achterkant)
- 61 cm (24in) voor toegang tot de deur, die naar links opent
- 5 cm (12in) van de rand van een open deur tot de volgende machine
- Fuse Sift afmetingen: diepte(61cm) x H(188,8 cm) x W(99,1 cm) (24in x 61,8in x 39in)
- Tussenruimte voor de Fuse Sift:
- 20 cm (8in) afstand van elke muur (zij- en achterkant)
- 61 cm (24in) voor toegang aan voorzijde, links, en rechts (voor vacuüm, poedercartridges, enz.)
In een ruimte van 4,56 m breed (van links naar rechts gemeten) kun je twee afzonderlijke Fuse 1 ecosystemen kwijt: twee Fuse 1-printers en twee Fuse Sift-units.
Het elektrisch vermogen van deze SLS printer
Omdat de Fuse 1 en de Fuse Sift gebouwd zijn met het oog op compactheid en efficiëntie, vereisen ze niet hetzelfde hoge elektrische vermogen als andere SLS-systemen. Hoewel je voor elke machine één circuit (stroomkring) nodig hebt, is het benodigde wattage algemeen beschikbaar en gemakkelijk te installeren.
Je hebt nodig:
- Twee onafhankelijke circuits die elk 120 volt en minstens 15 ampère leveren aan een NEMA 5-20R-stopcontact.
- De Fuse 1 en de Fuse Sift mogen geen enkel stroomkring delen met elkaar of met andere apparaten.
Als jouw vacuüm meer dan 12 ampère vraagt, heeft jouw Fuse Sift een onafhankelijk circuit nodig dat 120 volt en 20 ampère levert aan een NEMA 5-20R-stopcontact.
Verbinding met de Fuse 1: internet, software en dashboard
De Fuse 1 en Fuse Sift zijn eenvoudig toe te voegen aan jouw bestaande netwerk en zijn uitgerust met zowel ethernet- als WiFi-mogelijkheden. Nieuwe SLS-gebruikers hoeven geen dure software te kopen voor het beheer van de printers - de Fuse 1 en Fuse Sift zijn geïntegreerd in Formlabs' gratis, CAD-agnostische printoriëntatie-software PreForm.
PreForm maakt het ook gemakkelijk om het poedergebruik te optimaliseren (en zo de bedrijfskosten te minimaliseren) dankzij het automatische verpakkingsalgoritme, dat ervoor zorgt dat elk onderdeel zodanig in de bouwkamer wordt genest dat het ongesinterde poeder en de verspilde ruimte tot een minimum worden beperkt.
Er zijn ook directe integraties voor programma's als Fusion 360, zodat het integratie- en printvoorbereidingsgedeelte van jouw workflow naadloos en tijdbesparend verloopt. Voor bedrijven die hun SLS-productie hebben opgeschaald, is het beheer van poeder- en onderhoudsschema's, het op afstand starten van prints en het delen van bestanden en printvoortgang met jouw team eenvoudig via Dashboard mogelijk, een gratis online platform.
De binderjet-technologie die aan de basis ligt van de Shop- en Production-systemen van Desktop Metal biedt velerlei voordelen voor fabrikanten. Zo kan men snel zonder gereedschap complexe onderdelen produceren om fijne details te creëren, of honderden of zelfs duizenden onderdelen in één enkele printgang printen zonder dat er gereedschap voor nodig is. De bevindingen die we graag delen zijn overduidelijk: binderjet-onderdelen bieden veel voordelen voor de metaalverwerkende industrie. In deze blog vertellen wij je hier meer over.
Materiaaleigenschappen van binderjet-onderdelen
De materiaaleigenschappen van de onderdelen zelf zijn misschien wel het belangrijkst. Beide systemen printen onderdelen die voldoen aan de ASTM-normen (American Society for Testing and Materials) en de MPIF-normen (Metal Powder Industries Federation), of deze zelfs overtreffen. Zeker voor wat betreft de voornaamste kenmerken zoals sterkte, vervormbaarheid en hardheid. Dit maakt ze ideaal voor allerlei toepassingen: van juwelenfabricage tot de zware industrie.
Het bereiken van deze onovertroffen eigenschappen is mogelijk omdat de verdichtingstechnologie die door zowel het Shop- als het Production-systeem wordt gebruikt, is gebaseerd op de gevestigde en goed begrepen processen die in de conventionele poedermetallurgie en vooral bij het spuitgieten van metaal (MIM) worden gebruikt.
De MIM-basis van binderjetting is essentieel, omdat het de vorm van de onderdelen loskoppelt van hun metallurgie. Onderdelen worden gevormd op de printer met poeders die gemakkelijk verkrijgbaar zijn door hun overeenkomsten met gas-geatomiseerde MIM-poeders. De onderdelen worden vervolgens gebonden en verdicht tijdens het sinteren, net als MIM-onderdelen. Zo kunnen fabrikanten vrijwel elke geometrie creëren, met uitstekende eigenschappen voor de resulterende onderdelen.
[Isotropische microstructuur]
17-4PH geprint op het Production System
De scheiding tussen de wijze waarop de onderdelen worden gevormd en hun metallurgie is een belangrijk onderscheid ten opzichte van andere 3D-printbenaderingen, met name op laser gebaseerde metaalsystemen.
Deze systemen gebruiken lasers met een hoog vermogen om metaalpoeder te smelten, waarbij sporen van de vormingsmethode worden achtergelaten. De korrelstructuur van poedersmeltdelen heeft vaak een korreltextuur als gevolg van de directionele stolling van het onderdeel. Verder kunnen de herhaalde opwarmings- en afkoelingscycli en de temperatuurgradiënt over een onderdeel ook een enorme invloed hebben op de mechanische eigenschappen van het onderdeel. Ook kunnen ze aanleiding geven tot restspanningen die zowel de dimensionale als de mechanische eigenschappen kunnen beïnvloeden. Legeringen die faseovergangen ondergaan (zoals de overgang van austeniet naar ferriet in koolstof- en gereedschapsstaal) kunnen bijzonder hoge restspanningen en vervormingen vertonen als een deel van het onderdeel zich onder de overgangstemperatuur bevindt terwijl een ander deel zich boven de overgangstemperatuur bevindt. Om dit tegen te gaan, zijn voor poederbedfusie-onderdelen vaak spanning-reducerende processen nodig om de opgebouwde spanningen in het onderdeel als gevolg van dit niet-uniforme temperatuurproces te reduceren.
In vergelijking worden binderjet-onderdelen tijdens het sinteren gelijkmatig verhit en afgekoeld, waardoor een veel homogenere structuur ontstaat die vrij is van restspanningen. Een dwarsdoorsnede van een onderdeel toont een uniforme korrelgrootte en vorm, ongeacht de richting. De mechanische eigenschappen in X-Y-Z kunnen zeer uniform zijn, zoals blijkt uit onderstaand figuur. Deze staven zijn getest met bewerkte oppervlakken.
[Mechanische eigenschappen]
17-4PH van het Production System
Sterkte en vervormbaarheid van binderjetting-onderdelen
Twee belangrijke kenmerken voor eindgebruiksonderdelen, sterkte en vervormbaarheid, zorgen ervoor dat de onderdelen niet alleen bestand zijn tegen de krachten waaraan ze worden blootgesteld, maar - indien gewenst - ook elastisch kunnen vervormen (trek en buiging) alvorens te bezwijken.[Materiaaleigenschappen]
In tests overtreffen zowel gesinterd als warmtebehandeld binderjet-gespoten 17-4PH roestvast staal de MPIF-normen.
[Elasticiteit]
Desktop Metal binder-jetted 17-4PH vertoonde met name aanzienlijk meer elasticiteit dan metalen spuitgietonderdelen. Die vervormbaarheid kan uiterst voordelig zijn voor diverse toepassingen.
De metalen ringen in een parachute zijn een goed voorbeeld van waarom beide kenmerken essentieel zijn voor metalen onderdelen. Uiteraard moeten ze sterk genoeg zijn om de krachten van het openen van de parachute en het gewicht van de drager te kunnen weerstaan. De vervormbaarheid geeft de ringen bij grotere spanningen echter meer rek. Zo kunnen de ringen onder extremere omstandigheden worden gebruikt.
[Voorbeeld van vervormbaarheid]
Harnasringen van een parachute
Desktop Metal Additive Manufacturing 2.0 maakt 3D metaalprinten toegankelijk voor bedrijven die mede met hun kostprijs moeten concurreren, stelt Desktop Metal CTO Jonah Myerberg. Daarmee vult het Amerikaanse concern de ontbrekende stap naar digitale productie in. Reshoring en het tekort aan vakmensen staan plots in een heel ander perspectief.
Lights out factories: dat is het ultieme doel van de maakindustrie. Met automatisering en robotisering is de industrie al ver in deze richting opgeschoven. De ontbrekende schakel is de fysieke productie van componenten vanuit een digitaal model. Traditionele productietechnieken zoals CNC verspanen, persen en gieten hebben hun beperkingen, zoals de beperkte vormvrijheid, het instellen van machines, het materiaalverlies én het feit dat mass customization niet kan omdat dan de kosten te hoog oplopen. “Met Additive Manufacturing kunnen we deze stap wel zetten. AM is een digitaal proces; vanuit het 3D model gaan we direct naar het fysieke onderdeel, zonder tooling”, zegt Jonah Myerberg, co-founder en CTO van Desktop Metal. De AM-technologie van Desktop Metal zorgt hierbij voor de snelheid om daadwerkelijk naar volumeproductie te gaan. “Additive Manufacturing 2.0 betekent de transitie van prototypes en enkelstuks printen naar serieproductie met Additive Manufacturing.”
Waarom is binder jetting snel?
De geavanceerde printkoppen van de Desktop Metal metaalprinters Shop System en Production System zorgen in combinatie met de gepatenteerde Single Pass Jetting technologie voor de snelheid in het 3D printproces en daarmee voor lagere cost per part. In deze koppen zitten 70.000 nozzles verdeeld over 5 rijen. Daarmee kan het bindmiddel sneller en nauwkeuriger op het poederbed worden gejet. Desktop Metal doet hier met de gepatenteerde Single Pass Jetting technologie nog een schepje bovenop. Het aanbrengen van de nieuwe poederlaag en het jetten van het bindmiddel gebeuren in één beweging. In plaats van vectorbanen printen, printen de machines van Desktop Metal een volledige laag in één keer. Hierdoor is de technologie 100 keer sneller dan vector gebaseerde AM-technieken, zoals Powderbed Fusion. “We printen onderdelen in uren in plaats van dagen. Dat betekent massaproductie”, zegt Jonah Myerberg. Daarbij maakt het voor het systeem niks uit of de buildbox vol zit met honderden identieke onderdelen of producten die geometrisch verschillen van elkaar. “Wij zijn geometrisch agnostisch als we 3D printen.”
Robuuster sinterproces
Een tweede beslissende doorbraak die Desktop Metal gerealiseerd heeft, is het vereenvoudigen van het sinterproces. De binder jetting systemen produceren ‘groene’ onderdelen, net als bij MIM (Metal Injection Molding). Hierin houdt het bindmiddel het poeder bijeen. Na het verwijderen van los poeder worden de onderdelen in een oven gesinterd. De warmte wordt heel gecontroleerd in het werkstuk gebracht waardoor materiaaldichtheden tot meer dan 99% ontstaan. Er ontstaan geen restspanningen. Wel krimpen de onderdelen. De Live Sinter software van Desktop Metal compenseert automatisch hiervoor. Met deze software kan zelfs vooraf gecompenseerd worden voor eventuele vervormingen. Jonah Myerberg: “Omdat we de beperkingen van binder jetting goed begrijpen, kunnen we met Live Sinter, een FEM analyse tool (Eindige Elementen Methode), vooraf aanpassingen doen aan het 3D model om direct een maatvast onderdeel te printen en sinteren.” Deze software is nog lang niet uitontwikkeld, aldus de CTO van Desktop Metal. Het proces zal nog robuuster worden.
Game changer
Jonah Myerberg ziet de AM-technologie van Desktop Metal als een game changer die de maakindustrie eens in de veertig, vijftig jaar meemaakt. “De ware kracht van AM 2.0 is dat we de toelevering van onderdelen robuuster en betrouwbaarder maken. Met reshoring halen we spanningen uit de toeleveringsketens weg.” OEM’s en maakbedrijven kunnen activiteiten terughalen naar hun eigen regio, omdat ze minder afhankelijk worden van de beschikbaarheid van geschoolde operators. “Met AM 2.0 houdt één ervaren operator een hele fabriek draaiende. Zo worden supply chains minder afhankelijk van onzekere variabelen.” Met name het Shop System leent zich voor de toeleveringsindustrie omdat het een echte plug and play oplossing is waarvoor Desktop Metal de materialen en de instellingen levert. “Daags na de installatie print je ermee.”
Concurrerende technologie
De mechanische eigenschappen van de geprinte onderdelen liggen hoger dan die van gietstukken. Deze eigenschappen zullen verder verbeteren doordat momenteel met name in Europa materialen specifiek voor de technologie worden ontwikkeld. Qua kostprijs concurreert de technologie bij bepaalde applicaties al met gieten en zelfs CNC-frezen, zeker als de series klein zijn. En de voordelen zullen alleen maar groter worden naarmate engineers meer specifiek voor Additive Manufacturing gaan ontwerpen. Jonah Myerberg: “Velen herkennen de meerwaarde van Additive Manufacturing, maar ze weten nog niet hoe te designen voor AM. Complexe geometrieën, ondersnijdingen, het consolideren van meerdere losse componenten in één onderdeel: dat maakt Additive Manufacturing aantrekkelijk.”
Tweede generatie machines
De beperking is tot nog toe de afmetingen: maximaal 5 à 10 centimeter. Johan Myerberg verwacht echter dat deze afmetingen de komende jaren met een factor 4 tot 5 gaan toenemen als Desktop Metal de tweede generatie van Shop en Production System op de markt brengt. Kun je dan niet beter wachten met investeren totdat de nieuwe generatie productierijp is? Nee, zegt de CTO. Als de huidige applicatie qua geometrie en complexiteit maakbaar is, stap dan nu in om de technologie te doorgronden, adviseert hij. “De volgende generatie van onze machines wordt geen vervanging van de huidige maar een aanvulling.” Ze zullen de bestaande systemen over enkele jaren absoluut niet overbodig maken. “De toekomstige AM-systemen openen nieuwe markten, waar de huidige systemen nog niet rijp voor zijn.”
Automobielindustrie
De laagdrempeligheid van de twee AM-systemen van Desktop Metal biedt zowel de automotive industrie als de bredere machinebouw industrie toegang tot Additive Manufacturing. Vanwege de hoge kosten van Laser Powderbed Fusion, bleef 3D metaalprinten tot nog toe vooral beperkt tot lucht- en ruimtevaartbedrijven waar de kostenefficiënctie op een heel ander niveau ligt. “Met binder jetting brengen we kosten naar het niveau van andere productietechnieken, zonder dat je in gereedschappen hoeft te investeren én met de mogelijkheid van mass customization. Zo 3D print BMW al onderdelen voor de M-serie modellen. En ze pushen de techniek nu bij hun Tier 1 en 2 toeleveranciers.”
Desktop Metal en Nederland
Desktop Metal heeft het Europese distributiecentrum in Amsterdam gevestigd. In Nederland zitten ook enkele Shop System-klanten van het eerste uur. “Nederland is een belangrijke groeimarkt voor ons”, zegt Jonah Myerberg. Dat meet hij ook af aan het succes van Layertec, de Gold partner van het Amerikaanse concern in de Benelux. “Layertec boekt succes in de Nederlandse markt met hun aanpak om klanten volledig te ondersteunen.” Goede voorbeelden zijn de 1-daagse introductietraining ‘Ontwerpen voor 3D printen’ en de uitgebreide 3-daagse training om te leren ontwerpen voor Additive Manufacturing met SOLIDWORKS.
Het Desktop Metal Production System is ontworpen als de snelste manier om metaalonderdelen additief te vervaardigen. Het systeem ontleent zijn snelheid aan een verzameling technologieën die samen Single Pass Jetting™ worden genoemd.
Het productiesysteem is in essentie een binderjetting-systeem. Binder jetting is een relatief eenvudig proces welke is uitgevonden in de late jaren '80 in de laboratoria van MIT door Ely Sachs, één van de oprichters van Desktop Metal. Alle binderjetsystemen voeren vergelijkbare stappen uit om 3D-geprinte metalen onderdelen te maken.
In deze blog gaan we dieper op Single Pass Jetting in.
Het proces van binder jetting
In deze alinea leggen we uit hoe de basisprincipes in binder jetting werken om de vergelijking met Single Pass Jetting te kunnen maken.
1. Eerst wordt vers poeder op het printbed aangebracht. Er zijn verschillende manieren om deze stap uit te voeren. Sommige printers gebruiken een zogenaamde "bed-to-bed" poederdosering, waarbij het poeder wordt aangevoerd door een aanvoerzuiger, en dat poeder vervolgens bovenop het printbed wordt geduwd. Een andere mogelijkheid is dat het poeder van bovenaf wordt gedoseerd en dat de doseerinrichting over het bed wordt verplaatst om het poeder te verdelen.
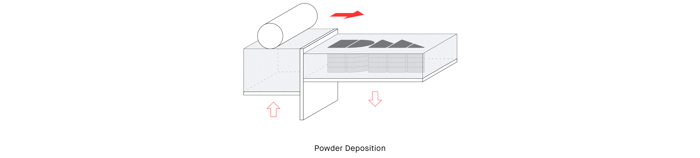
2. Vervolgens wordt het vers gedeponeerde poeder gelijkmatig over het bed verspreid en ietwat verdicht. Vibrerende messen en contra-roterende rollen zijn twee voorbeelden van de gebruikelijke manieren waarop dit kan worden uitgevoerd.
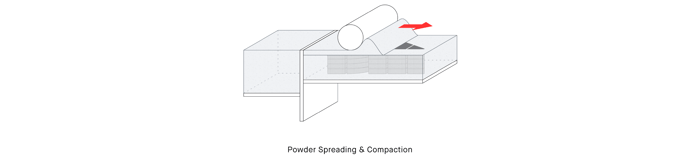
3. Nu is het poederbed klaar voor de toevoeging van het bindmiddel. Het bindmiddel wordt meestal met inkjettechnologie in een patroon op het bed aangebracht. Een of meer inkjetprintkoppen vormen een reeks spuitkoppen die de druppels precies daar kunnen spuiten waar het bindmiddel nodig is. Tijdens deze stap wordt die spuitkop in ten minste één richting over de build box verplaatst. Het is van cruciaal belang dat elke pixel benaderbaar is. Als de spuitkop korter is dan de build box OF als de printkoppen een lagere native resolutie hebben dan de gewenste printresolutie, is het noodzakelijk om de spuitkoparray in twee richtingen te verplaatsen om het printen te voltooien (zoals hieronder geïllustreerd).
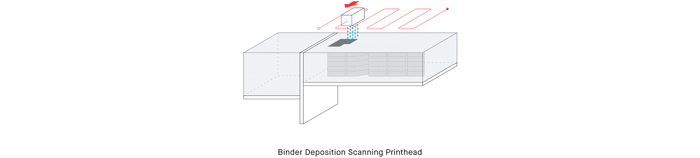
4. Een laatste (en soms optionele) stap is het drogen of nabehandelen van het bed waarop het natte bindmiddel is aangebracht.
[De vierde stap in het proces is het drogen van het natte bindmiddel]
Deze stappen worden dan herhaald voor de volgende laag, en het proces herhaalt zich tot de build voltooid is.
Alle binderjetsystemen maken gebruik van processtappen die vergelijkbaar zijn met als hiervoor beschreven, hoewel er een groot aantal variaties bestaat. Wanneer de stappen serieel en via een afzonderlijke beweging van componenten worden uitgevoerd, moet elke stap worden voltooid voordat de volgende kan beginnen. Deze aanpak is typerend voor binder jetting, met als gevolg dat het 20 seconden of meer duurt om elke laag te voltooien. Dat klinkt snel, maar voor één enkele build box kunnen duizenden lagen nodig zijn. Voor zeer dunne lagen neemt het aantal lagen (en de tijd om de build box af te werken) evenredig toe.
Tegenwoordig evenaren de materiaaleigenschappen van binderjet-onderdelen die van hun traditioneel vervaardigde tegenhangers, of overtreffen ze zelfs. Toch zijn er enkele cruciale manieren waarop ze verschillen. Afhankelijk van hoe ze gevormd zijn, kunnen 3D geprinte metalen onderdelen zichtbare opbouwlagen vertonen of scherpe randen hebben. Bovendien hebben ze een aanzienlijk hogere oppervlakteruwheid dan onderdelen die geslepen, gefreesd of gedraaid zijn. Hoewel veel toepassingen voor metalen 3D-geprinte onderdelen geen nabewerking vereisen, zijn de mogelijkheden voor de onderdelen die dat wel vereisen enorm.
Afgezien van het corrigeren van kleine onvolkomenheden zijn er tal van redenen om onderdelen na te bewerken. Dit kan de noodzaak zijn om ervoor te zorgen dat de onderdelen de juiste eindafmetingen hebben, het gladmaken van interne kanalen om de doorstroming te verhogen of er kunnen esthetische overwegingen spelen.
In deze blog delen wij verschillende nabewerkingsmogelijkheden voor metalen 3D-geprinte onderdelen.
Het ‘groen’ schuren van metalen 3D-geprinte onderdelen
Schuren is een ideale oplossing voor het verminderen van de zichtbaarheid van printlagen en andere oppervlakte-imperfecties. Dit geldt vooral voor extrusie-gebaseerde printmethodes. Het zogenoemde ‘groene’ schuren vindt plaats direct nadat de onderdelen zijn geprint, wanneer het metaalpoeder alleen nog door polymeerbindmiddelen bij elkaar wordt gehouden.
Aangezien groene onderdelen relatief zacht zijn – hun consistentie komt overeen met die van een krijtje – kan een eenvoudige Scotch Brite-pad worden gebruikt om kleine onvolkomenheden, zoals laaglijnen, glad te maken. Meer agressief schuurwerk kan worden gedaan met schuurpapier en een scheermes kan worden gebruikt om randen schoon te maken.
Hoewel ze veel gemakkelijker te bewerken zijn dan gesinterde metalen onderdelen, betekent de zachte consistentie van groene onderdelen dat men voorzichtig te werk moet gaan om beschadiging te voorkomen.
De voordelen van groen schuren kunnen echter aanzienlijk zijn. Groen geschuurde onderdelen hebben doorgaans een drie- tot vijfmaal fijnere oppervlakteafwerking dan ongeschuurde onderdelen. Afhankelijk van de toepassing kan de nabewerkingstijd tot tien keer korter zijn voor nabewerkte metalen onderdelen.
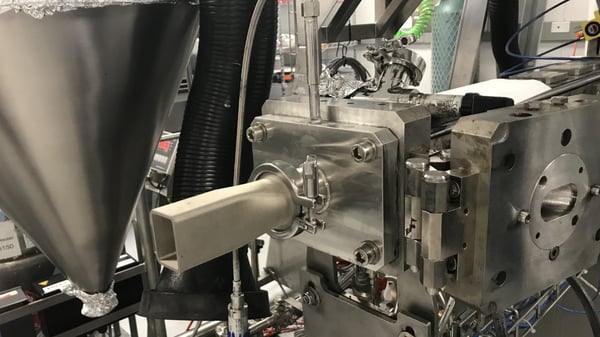
Stralen als nabewerkingsoptie
Bij het stralen wordt perslucht gebruikt om een straalmiddel, zoals aluminiumoxide, roestvrij staal of glasparels, tegen het onderdeeloppervlak te blazen en zo een gelijkmatige matte of glanzende afwerking te verkrijgen.
Het straalmiddel is ideaal voor het verwijderen van verkleuringen of het wegwerken van oppervlaktekrassen en gereedschapssporen. Het verandert de maatnauwkeurigheid van de onderdelen niet en kan in slechts enkele minuten worden uitgevoerd.
Door de luchtdruk aan te passen, kan ook de agressiviteit van het straalproces worden gewijzigd. Met een lagere druk kan de oppervlaktekleur van een onderdeel worden veranderd, terwijl met staalkogels of glasparels bij een hogere druk het oppervlak zelfs kan worden ontbraamd.
Als bijkomend voordeel – helemaal wanneer glazen kogeltjes worden gebruikt – is het proces heel milieuvriendelijk. Het reinigen en hergebruiken van de kogeltjes is zeer eenvoudig.
Trommelen van metalen 3D-geprinte onderdelen
Trommelen omvat een groep processen waarbij machines met lage energie en willekeurige bewegingen worden gebruikt om in combinatie met media en schuurmiddelen het oppervlak van onderdelen uitsluitend mechanisch te verfijnen.Hoewel deze nabewerkingsmethode kan worden ingezet voor zowel grote als kleine onderdelen, is trommelen het meest geschikt voor onderdelen met een relatief eenvoudige geometrie.
Wanneer het wordt toegepast op complexere geometrieën, kan trommelafwerking resulteren in niet-uniforme afwerkingen.
Pin finishing als nabewerkingsoptie
Pin finishing is een vorm van trommelen die ideaal is voor de goedkope nabewerking van kleinere onderdelen.Bij dit proces worden krachtige magneten gebruikt om een metalen medium en de na te bewerken onderdelen in een cirkelvormige beweging te brengen. Terwijl het medium en de onderdelen tegen elkaar schuren, worden de onderdelen ontbraamd.
Trillen
Trillen is een batchproces dat meestal wordt toegepast op grote aantallen en relatief kleine onderdelen. De onderdelen worden in de kuip van een triltrommel geplaatst met abrasieve middelen in verschillende vormen.Door de trillende werking van de kuip schuurt het middel tegen de onderdelen, verwijdert bramen en laat ze gepolijst, schoon en glanzend achter.
Afhankelijk van de toepassing en de samenstelling van het slijpmiddel kan het proces nat of droog zijn, en kan het zeer zacht of zeer agressief zijn.
Om de operator in staat te stellen om gemakkelijk te zien wanneer de gewenste afwerking is bereikt, wordt het proces meestal uitgevoerd in een open kuip.
De Formlabs Fuse 1 geeft de engineers die testopstellingen ontwikkelen aan de TU Delft nog meer designvrijheid dan ze gewend waren van 3D printen. Het feit dat de dienst DEMO nu SLS-technologie in eigen huis heeft, verkort bovendien doorlooptijden enorm. In plaats van uitbesteden en twee weken wachten, zijn de onderdelen nu 24 uur later beschikbaar om te evalueren of te testen.
Met 85 medewerkers is de Dienst Elektronische en Mechanische Ontwikkeling (DEMO) het ingenieursbureau van de TU Delft. Hier ontwikkelen engineers de hardware en elektronica, waarmee de wetenschappers hun onderzoeken uitvoeren. “Dat kan een eenvoudig bakje zijn tot en met een opstelling met meerdere gemotoriseerde assen die een miljoen euro kost”, zo schetst Ernst van der Wal, teamleider op de DEMO-locatie bij de faculteit Natuurkunde, de breedte van de opdrachten die DEMO uitvoert. Er wordt gewerkt met de gangbare productietechnieken, met name CNC-frezen en draaien en sinds zo’n 10 jaar 3D printen. Deze laatste technologie wordt alsmaar belangrijker. De nieuwe mogelijkheden die 3D printen biedt, is de grootste drijfveer. “Vooral vanuit ontwerpperspectief en het feit dat we snel kunnen itereren.”
SLS printen met de Fuse 1 geeft ons nog meer ontwerpvrijheid
Fuse 1: meerdere voordelen
DEMO beschikt ondertussen over verschillende 3D printtechnieken: FDM (Ultimaker en Prusas), SLA (Form 2, 3 en 3L printers), twee metaalprinters (Sisma en DMG) en sinds kort SLS. De ontwikkelafdeling van de TU Delft heeft namelijk in een Formlabs Fuse 1 geïnvesteerd. “De Fuse 1 geeft ons nog meer ontwerpvrijheid doordat er geen support nodig is”, zegt Kevin Kamman, ontwikkelingstechnicus en verantwoordelijk voor het 3D printen met de nieuwe SLS-printer. “Daarnaast printen we meteen een hoogwaardig nylon (PA12) product, dat we eventueel kunnen nafrezen of -draaien voor een nauwkeurige passing. En de onderdelen ogen professioneler.” De vormvrijheid stelt de DEMO-engineers in staat om met hun ontwerpen de grenzen verder te verleggen, bijvoorbeeld qua topologie optimalisatie, complexe structuren en functie-integratie, zoals verende elementen mee printen. “De sky is the limit.”
De samplehouder die als monodeel is geprint.
Kevin Amman toont een voorbeeld van een complex prototype van een samplehouder voor het positioneren in een neutronenbundel, bestaande uit een frame met daarin een verende ophanging. De houder is 3D geprint als monodeel. Met geen enkele andere technologie zou dit zo gemaakt kunnen worden. Dankzij de beschikbaarheid van de Fuse 1 kon het idee een dag later al samen met de wetenschapper beoordeeld worden. Een ander voorbeeld is een prototype van een spoed voor magneetwikkelingen. “Bij FDM trad delaminatie op door de kracht op het onderdeel; de onderdelen geprint met de Form 3 waren te bros. Met de Fuse 1 ging het in een keer goed, Nylon heeft de perfecte eigenschappen.”
De Desktop Metal Shop System en Production System zijn de eerste Additive Manufacturing-systemen die voordelen bieden zoals massaproductie van functionele onderdelen voor eindgebruik, mass customization en productie zonder gereedschap. Ze zijn daarmee perfect voorgesorteerd om een ware productierevolutie te ontketenen. Desktop Metal noemt dit Additive Manufacturing 2.0.
De kern van beide systemen wordt gevormd door binder-jetting, een technologie die additive manufacturing in staat stelt om op diverse fronten te concurreren met conventionele massaproductiemethoden, waaronder snelheid.
In deze blog vertellen wij je waarom binder jetting de ideale oplossing is voor veel bedrijven.
Tot 100 keer sneller produceren
Met een constructie die gebaseerd is op inkjetprintkoppen – vergelijkbaar met de printkoppen die in miljoenen thuisprinters wordt gebruikt – kunnen binderjet-printers onderdelen tot 100 keer sneller produceren dan laserpoederbed-fusiesystemen.
Dankzij die snelheid kunnen binderjet-systemen kosten per onderdeel opleveren die kunnen concurreren met conventionele processen zoals gieten en smeden. Maar snelheid is slechts één van de vele voordelen.
Binderjetting biedt ook veel van de traditionele 3D-printing voordelen. Denk aan de mogelijkheid om complexe geometrie te creëren, met inbegrip van inwendige features en kanalen, het gebruikmaken van topologieoptimalisatie en generative design, of assemblage-consolidatie waarbij diverse functies in één onderdeel worden gecombineerd.
Combineer deze voordelen met de snelheid van binderjetten en het potentieel van Additive Manufacturing 2.0 komt écht binnen handbereik.
Nauwkeurig 3D metaalprinten met binder jetting
Binderjet-systemen zijn niet alleen snel in staat om complexe vormen te produceren, ze zijn ook ongelooflijk nauwkeurig.
Met een native resolutie van 1200 dpi is het Shop System het binderjet-systeem met de hoogste resolutie dat op de markt verkrijgbaar is. Het systeem kan maar liefst 670 miljoen binderdruppels per seconde produceren. Die precisie maakt het vervaardigen van onderdelen mogelijk, zoals dit zeer gedetailleerde tondeuseblad, zonder dat dure gereedschappen nodig zijn.
Het Production System combineert een resolutie van 1200 dpi en laaghoogtes van slechts 50 µm met een unieke Single Pass Jetting-methode die elke beweging van de printkop benut om laagdikte op te bouwen.
Het resultaat is een systeem dat niet alleen nauwkeurig genoeg is om een rand van een horloge met zeer fijne details te printen, maar ook snel genoeg is om er 1.200 in één keer te produceren tegen een kostprijs van slechts €1,04.
Mogelijkheid tot serieproductie met binder jetting
Net als andere 3D-printbenaderingen, maakt het feit dat binderjetting zonder gereedschap werkt het eenvoudig om ontwerpen aan te passen.
In tegenstelling tot andere benaderingen, maakt binder jetting ook serieproductie mogelijk. Fabrikanten kunnen meerdere versies van één onderdeel in één print produceren, wat uiteindelijk helpt om de kosten van onderdelen te verlagen.
De vooruitgang op het gebied van 3D-printen blijft de manier veranderen waarop bedrijven prototyping en productie benaderen. Naarmate de technologie toegankelijker en betaalbaarder wordt en de hardware en materialen worden aangepast aan de marktkansen en -eisen, integreren steeds meer ontwerpers, ingenieurs en anderen 3D-printing in de workflows van alle ontwikkelingstrajecten. In alle sectoren helpt 3D-printen professionals om uitbestedingskosten te verlagen, sneller te innoveren, productieprocessen te optimaliseren en zelfs geheel nieuwe bedrijfsmodellen te ontsluiten.
In deze klantcase bespreken we Antoni van Leeuwenhoek, het in kanker gespecialiseerde ziekenhuis en onderzoeksinstituut.
3D printen is niet meer weg te denken in de zorg voor de oncologie-patiënten van het Antoni van Leeuwenhoek ziekenhuis. Met de modellen en boor- en zaagmallen kunnen chirurgen ingrepen beter plannen en uitvoeren. Ze kunnen risico’s van een ingreep uitleggen aan de patiënt. En als het nodig is, worden de Formlabs SLA-printers gebruikt om mallen te printen voor het maken van prothesen. Dat scheelt tijd, bezoeken aan het ziekenhuis en levert een betere pasvorm.
Chirurgen van het Antoni van Leeuwenhoek doen vier tot vijf prostaatoperaties in de week. Tegenwoordig allemaal met de Da Vinci robot. De chirurg zit in een hoek van de OK, kijkt naar het beeldscherm met daarop het 3D beeld van de buikholte van de patiënt en stuurt met een joystick de robot aan. Nauwkeuriger dan met de hand mogelijk is.
Dikwijls heeft de chirurg een 3D geprint model van de prostaat met de tumor bij de hand. Hierop is de locatie van de tumor in de prostaat zichtbaar. Dankzij zo‘n model kan de chirurg de uitkomst van de prostaatresectie vooraf beter inschatten. “En het is fijn als hij een fysiek model bij de hand heeft tijdens de operatie”, zegt Maarten van Alphen, klinisch technoloog. Omdat de chirurg in een hoek van de operatiekamer zit, hoeft het model niet steriel te zijn. Maarten van Alphen werkt net als Robert van Veen, toegepast natuurkundige, als post-doc onderzoeker bij het ziekenhuis. Beide zijn oprichter van het Verwelius 3D Lab.
Toename van toepassingen
Het 3D printen van fysieke modellen is slechts een van de vele toepassingen waarvoor het Verwelius 3D Lab de Formlabs SLA-printers inzet. Vijf jaar geleden heeft het in oncologiebehandeling gespecialiseerde ziekenhuis het 3D Lab geopend. In de begintijd ging het met name om het in beeld brengen en plannen van resecties (correcties) van gedeelten van de onderkaak. Hierbij werd toen ook een 3D model van de onderkaak geprint. Maarten van Alphen: “Als je de titanium platen kunt voorbuigen op een model, kun je veel werk vooraf doen en zorg je dat dit niet op de OK hoeft te gebeuren.” Inmiddels is het werkgebied van het 3D Lab verbreed.
Hoofd- en hals chirurgie maakt er gebruik van, net als urologie, thoraxchirurgie en radiotherapie. In het 3D Lab werken daarnaast voortdurend zes, zeven studenten Klinische Technologie van de universiteiten Twente en Delft. Ook zij gebruiken de 3D printers voor hun onderzoeken. Er lopen 7 onderzoekslijnen en 14 projecten.
Snelheid door in huis te 3D printen
De tijdwinst die het ziekenhuis boekt door in huis te printen, is belangrijk, leggen Maarten van Alphen en Robert van Veen uit. “Hierdoor kunnen we een model dezelfde dag aan de arts geven. De tijdwinst die het ziekenhuis boekt door in huis te printen, is belangrijk, leggen Maarten van Alphen en Robert van Veen uit. “Hierdoor kunnen we een model dezelfde dag aan de arts geven. We doen ook veel research naar genavigeerd zagen, dan is het handig als je snel een mock-up kunt printen met prototypes van de zaagmal."
Voor de studenten die aan onderzoeken werken om de behandelingsmethoden te verbeteren, is snelheid helemaal belangrijk. “Soms zijn ze maar tien weken hier. Twee weken op een externe leverancier wachten duurt te lang, afgezien van de rompslomp met bestelformulieren. Nu 3D printen ze hun model en kunnen dat vaak nog dezelfde dag aanpassen als het nodig is.”
Het Verwelius 3D Lab van het Antoni van Leeuwenhoek ziekenhuis gebruikt hiervoor drie low force stereolithografie printers van Formlabs: naast twee Form 3B printers ook een Form 3BL, met een extra groot bouwvolume. Dit grote formaat is nodig voor de productie van mallen, waarmee via enkele tussenstappen aangezichts- prothesen worden gemaakt. Soms moeten de chirurgen bij een patiënt een oog uitnemen, af en toe met zelfs een deel van het gezicht; soms amputeren ze oren.
Vroeger werden de prothesen voor deze patiënten volledig met de hand gemaakt. Alleen al het maken van de vorm die nodig is voor verloren was gieten, kon tot wel 12 uur duren. Bovendien moest de patiënt meerdere keren naar het ziekenhuis komen.
Maarten van Alphen: “Nu scannen we het gezonde deel, spiegelen dit naar de andere zijde en daarmee hebben we binnen een half uur het 3D model voor de mal klaar.” Voor de patiënt betekent dit minder vaak naar het ziekenhuis gaan en de siliconenprothese heeft een betere pasvorm dankzij de optische scan en de geprinte mal.
De derde van een driedelige serie waarin de voordelen, prestaties en kostenbesparingen van het Shop System worden onderzocht.
Het Shop System is 's werelds eerste binder jetting systeem voor metaalbinders, speciaal ontworpen voor machinewerkplaatsen. Dit systeem kan complexe metalen onderdelen printen met de voordelen die standaard machinewerkplaatsen verwachten: een ongeëvenaarde productiviteit met een superieure printkwaliteit, waarbij de toegankelijkheid tijdens het gehele proces op een hoog niveau blijft.
Naast proces- en productinnovaties, uitzonderlijke productiviteit, printkwaliteit en betrouwbaarheid, biedt het Shop System nog een ander belangrijk voordeel, namelijk de mogelijkheid om zowel de kosten te verlagen als de inkomsten te verhogen.
De ongeëvenaarde productiviteit van het Shop System maakt het mogelijk om kosten per onderdeel te realiseren die concurrerend zijn met conventionele productiemethoden zoals gieten en smeden. Zo wordt het systeem een rendabele optie voor de productie van metalen onderdelen voor eindgebruik in velerlei industrieën en toepassingen. In deze blog vertellen wij je hier meer over.
Gereduceerde kosten door 3D metaalprinten
Omdat 3D-printen in metaal geen gereedschap vergt, hoeven fabrikanten de afschrijving van gereedschap niet door te berekenen in de kosten van het onderdeel. Voor grote hoeveelheden onderdelen leidt dit tot aanzienlijke besparingen per onderdeel, aangezien de gereedschapskosten vaak tot tienduizenden euro’s kunnen oplopen.
Hoewel bij machinale bewerking soms fors minder in gereedschap hoeft te worden geïnvesteerd, levert 3D metaalprinten toch een kostenbesparing op doordat er minder slijtage optreedt aan snijgereedschap. Bovendien bespaart je op arbeidskosten doordat er slechts een minimale inspanning nodig is van een operator.
Het printen vermindert ook het aantal productiestappen substantieel door onderdelen laag voor laag op te bouwen. Dit in tegenstelling tot verspanen, waar voor verschillende onderdelen meerdere machines en oriëntaties nodig kunnen zijn.
Ook kunnen hele constructies in slechts één tot twee uur worden opgezet, ongeacht het aantal onderdelen en de complexiteit. Het opspannen van elk te verspanen onderdeel moet daarentegen zorgvuldig worden overwogen en uitgevoerd, een proces dat uren vergt voor elke unieke geometrie.
Hogere inkomsten met 3D metaalprinten
Door het mogelijk te maken onderdelen te produceren met eigenschappen die tot voor kort onbereikbaar waren en onderdelen met verschillende geometrieën in serie te produceren, kan het Shop System machinewerkplaatsen helpen om nieuwe opdrachten binnen te halen en nieuwe inkomstenbronnen te ontsluiten.
Het systeem maakt het voor gebruikers ook gemakkelijk om snel en betrouwbaar de kosten van onderdelen te voorspellen en offertes te maken, waardoor werkplaatsen meer opdrachten kunnen binnenhalen.
Als er eenmaal orders binnenkomen, verkort het Shop System de doorlooptijden voor veel onderdelen aanzienlijk. Het printen kan vrijwel onmiddellijk beginnen en honderden onderdelen kunnen 's nachts worden geproduceerd, zodat de 3D-printers onderdelen in slechts enkele dagen aan klanten kunnen uitleveren en capaciteit kunnen vrijmaken voor nieuwe opdrachten.
Het elimineren van gereedschap en de mogelijkheid om gelijktijdig opdrachten te printen voor meerdere klanten in één enkele build maakt kleine en middelgrote opdrachten ook economischer. Zo kunnen fabrikanten van poedermetaal kleinere opdrachten aanbieden aan klanten tegen veel lagere kosten per onderdeel en kortere doorlooptijden. Dit betekent dat de kosten per onderdeel hetzelfde blijven, of je nu 1 of 1.000 onderdelen print.
De tweede van een driedelige serie waarin de voordelen, prestaties en kostenbesparingen van het Shop System worden onderzocht.
Het Shop System is 's werelds eerste binder jetting systeem voor metaalprinten, speciaal ontworpen voor machinewerkplaatsen.
Het systeem kan complexe metalen onderdelen 3D printen met de voordelen die machinewerkplaatsen verwachten: een ongeëvenaarde productiviteit met een superieure printkwaliteit, waarbij de gebruiksvriendelijkheid tijdens het gehele proces op een hoog niveau blijft.
Naast het ontsluiten van proces- en productinnovaties, is de binder jetting-technologie van het Shop System in staat om betrouwbare, hoge prestaties te leveren die voldoen aan de eisen van een moderne machinewerkplaats.
Dankzij de hoge capaciteit en flexibiliteit van het Shop System kunnen hoogwaardige, volledig dichte onderdelen in principe direct uit de sinteroven worden ingezet. Dit maakt het systeem tot een uitstekende productiekeuze voor kleine, middelgrote en grote volumes van eindtoepassingen.
Dit binder jetting systeem biedt veel voordelen voor verschillende bedrijven. In deze blog focussen we ons op de prestaties van dit systeem.
Ongeëvenaarde productiviteit in 3D metaalprinten
De innovatieve single-pass print techniek van het Shop System maakt een snelle productie van metalen onderdelen mogelijk. Omdat de printbalk de volledige breedte van het printbed omvat, kunnen volledige lagen van meerdere onderdelen in slechts enkele seconden worden geprint.
Dankzij die printsnelheid - tot 10x sneller dan laserpoederbedfusie-systemen - kan het Shop System een volledig bouwvolume printen in één shift van 6 tot 12 uur, afhankelijk van de hoogte van de build.
De printtijden zijn flexibel en worden bepaald door factoren zoals het formaat van de print en laaghoogte. Dit betekent dat gebruikers de printtijd eenvoudig kunnen aanpassen aan hun werkschema. Hierbij kan gedacht worden aan overdag een print van zes uur en ’s nachts de 3D printer om te schakelen naar een langere printduur met minimale belasting van de operator. Dit zorgt voor een optimale productiviteit met een zeer hoge bezettingsgraad.
Superieure printkwaliteit in 3D metaalprinten
Het Shop System print klant-en-klare onderdelen in hoge resolutie met ongelooflijk fijne details. Met een resolutie van 1600 x 1600 dpi (dots per inch) - 33% hoger dan concurrerende systemen – is het mogelijk om meer dan 670 miljoen druppels per seconde te produceren en laaghoogtes tussen 40um en 100um. Het systeem is daarmee het nauwkeurigste single-pass binderjetting-systeem op de markt in 3D metaal printing.
Om zowel fijne details als hoge printsnelheden te leveren, maakt het Shop System gebruik van een adaptieve print engine die 1,2pL druppels produceert en geautomatiseerde druppel-multiplexing tot 6pL. Dit resulteert in oppervlakteafwerkingen tot 4µm Ra, optimale controle over de afloop en fijne details. Dit alles met behoud van hoge printsnelheden.
Met de gebruikelijke nabewerkingsmethoden kan de oppervlakteafwerking nog verder worden verbeterd, tot minder dan 0,1 µm Ra. Bovendien komen de Shop System-onderdelen volledig dicht en isotroop uit de sinteroven en zijn ze meteen klaar voor eindgebruik.
Uitstekende betrouwbaarheid
Met meer dan 70.000 jets verdeeld over vijf rijen, biedt de Shop System-printbalk voldoende overlap om ervoor te zorgen dat eventuele jet-storingen (veroorzaakt door verstopte spuitmonden) niet resulteren in printfouten.
Ingebouwde, automatisch geprogrammeerde reinigingscycli zorgen ervoor dat de printkop altijd optimaal presteert gedurende zijn totale, verlengde levensduur. Dit zorgt voor een verbeterde printkwaliteit en hogere betrouwbaarheid.
De productiviteit, printkwaliteit en betrouwbaarheid van het Shop System vormen samen de ideale oplossing voor machine- en metaalwerkplaatsen die hun productiviteit willen verhogen met 3D-printen in metaal.
Met de mogelijkheid om tientallen tot honderden onderdelen te printen met toleranties die compatibel zijn met machinale bewerking, stelt het Shop System werkplaatsen in staat om nieuwe en grotere opdrachten van klanten aan te nemen. De uren van de bankwerkers komen nu beschikbaar voor het nog verder verfijnen van kritische onderdelen.
De eerste van een driedelige serie waarin de voordelen, prestaties en kostenbesparingen van het Shop System worden onderzocht.
Het Shop System is 's werelds eerste binder jetting systeem ontworpen voor machinewerkplaatsen om (complexe) metalen onderdelen te maken. Het systeem biedt een ongeëvenaarde productiviteit met een superieure printkwaliteit, waarbij de toegankelijkheid tijdens het gehele proces op een hoog niveau blijft.
De binder jetting-technologie die aan de basis ligt van het Shop System biedt fabrikanten tal van voordelen. In deze blog focussen we op zowel proces- als productinnovaties.
Procesinnovaties
Net als andere 3D-printmethoden vereist binder jetting geen tooling. Dit betekent dat onderdelen vaak sneller en betaalbaarder kunnen worden geproduceerd dan met conventionele productieprocessen. Maar in tegenstelling tot oudere 3D-printtechnologieën voor metaal zoals DMLS, SLS, SLM en EBM, kunnen deze onderdelen met binder jetting in grote volumes worden geproduceerd.
Zodra het ontwerp klaar is, kan het printen beginnen en kunnen honderden onderdelen in één nacht worden geprint. Dit in tegenstelling tot weken wachten op de fabricage van harde gereedschappen, iets wat gebruikelijk is bij traditionele fabricagemethoden.
Omdat de fabricage niet gebonden is aan een bepaald gereedschap, vereenvoudigt binder jetting het proces ontwerpwijzigingen aanzienlijk. Je kunt eenvoudigweg het CAD-bestand bijwerken en de nieuwe ontwerpen naar de printer sturen. Die mogelijkheid om ontwerpen naar behoefte aan te passen, biedt een ongekende ontwerpvrijheid.
Ook wordt het mogelijk om de prestaties van producten te verbeteren middels gespecialiseerde ontwerpen die precies kunnen worden afgestemd op de behoeften van de eindgebruiker.
Dit gereedschapsloze productieproces leidt tot een zeer flexibele productieomgeving, waardoor vaak minder opslagruimte en voorraden nodig zijn. Fabrikanten printen de onderdelen simpelweg snel wanneer ze die nodig hebben, en hoeven oude gereedschappen niet langer voor onbepaalde tijd op te slaan voor het geval ze nodig zijn. In plaats hiervan kunnen ze "digitale magazijnen" creëren om onderdeelbestanden op te slaan, en deze oproepen en printen wanneer nodig.
"Binder jetting blinkt echt uit. Het is voor ons als onderdeel van onze complexe serieproductie een goedkoop productieproces met een hoge opbrengst. Het stelt ons in staat om een nieuw paradigma te initiëren voor veilige, betrouwbare en koolstofvrije kernenergie.
Ultra Safe Nuclear Corporation (USNC) is een wereldleider in het toepassen van microreactoren en is bovendien een sterke verticale integrator van kernenergietechnologieën.
Het bedrijf zet zich in om veilige, commercieel concurrerende, schone en betrouwbare kernenergie naar energiemarkten over de hele wereld te brengen. Voor de innovatie en optimalisatie van kernreactoren maken ze gebruik van 3D printen van keramiek met de binder jetting techniek.
Next-generation kernenergie voor de toekomst
Meer dan een dozijn landen wereldwijd werken nu samen in een mondiale race om Generation IV - next-generation-concepten voor kernenergie. Deze concepten worden als essentieel beschouwd voor het leveren van koolstofvrije energie aan een wereld met een steeds grotere vraag naar elektriciteit. Dus geen gebruik van kolencentrales meer.
Terwijl hernieuwbare bronnen zoals zonne- en windenergie blijven groeien, heeft zich in energiekringen een conventionele wijsheid ontwikkeld dat kernenergie op zichzelf staat als een betrouwbare energiebron op basislastniveau. Dat is een bron die continu moet werken om 24 uur per dag en 7 dagen per week aan de minimumvraag naar elektriciteit te voldoen zonder negatieve gevolgen voor het milieu.
Dr. Kurt A. Terrani, Executive Vice President van de Core Division van USNC, werkt met geavanceerde technieken zoals binderjet 3D-printen om innovatieve onderdelen voor kernreactoren te produceren.
In dit speelveld levert USNC een baanbrekende bijdrage aan een groep innovatieve bedrijven die werken aan het op de markt brengen van geavanceerde nucleaire concepten. Hierbij zijn vaak nieuwe productiemethoden, zoals 3D-printen, nodig om geheel nieuwe ontwerpen te realiseren die optimale prestaties leveren op basis van unieke materialen.
Internationaal erkend expert op het gebied van splijtstoffen Dr. Kurt A. Terrani, voormalig Nationaal Technisch Directeur van het Oak Ridge National Laboratory (ORNL), heeft zich in februari 2020 aangesloten bij het team van USNC om de missie van het bedrijf naar een nog hoger plan te tillen. Hierin staat het veilige en gecontroleerde produceren van betrouwbare kernenergie op aanvraag centraal. Ongeacht waar in wereld die productie moet plaatsvinden. Terrani voorspelt dat kleine geavanceerde reactoren op basis van innovatieve brandstoffen en koelmiddelen - dus geen gigantische kerncentrales - een paradigmaverschuiving in kernenergie teweeg zullen brengen. Dit nieuwe paradigma heeft de wereld hard nodig, vooral nu.
"USNC opereert aan de frontlinie van splijtstof- en reactorontwerp en is een pionier op het gebied van veiligheid en prestaties", aldus Terrani. "Het opstarten van een nieuwe generatie microreactoren luidt een keerpunt in in de koolstofvrije energieproductie wereldwijd."
Fukushima ramp vs klimaatverandering
De reis van USNC begon in 2011; hetzelfde jaar waarin Japan door een inmiddels beruchte aardbeving werd getroffen. De kerncentrale van Fukushima Daiichi legde zoals voorgeschreven haar activiteiten stil. Vijftig minuten na de beving werd de centrale echter getroffen door een tsunami. Deze overspoelde en beschadigde nagenoeg alle generatoren die werden gebruikt om het koelwater in beweging te houden. Dit leidde tot een meltdown en de daaropvolgende explosie van drie reactoren.
Het tragische ongeval trof de nucleaire industrie in een toch al lastige periode. De hoge kosten van traditionele reactoren, in combinatie met andere ernstige ongevallen zoals in Tsjernobyl, vertraagde vooruitgang en deden vele landen tot ontmanteling besluiten. Tegelijkertijd kwamen veel regeringen tot de tegenstrijdige conclusie dat kernenergie eigenlijk een van de meest betrouwbare, draagbare en groene basisbronnen is.
De Verenigde Staten, de EU, Canada, Japan en vele andere staten en landen beschouwen kernenergie, waarbij geen CO2 vrijkomt, als onmisbare schakel in een duurzame energiemix, helemaal nu het mondiale elektriciteitsverbruik blijft toenemen.
Nu wisten vooraanstaande nucleaire deskundigen, waaronder Terrani, al geruime tijd dat er een betere manier is om veilige kernenergie te realiseren. De technologieën die destijds werden gebruikt in installaties zoals die van Three Mile Island en Fukushima dateerden uit de jaren vijftig en zestig. Veel geavanceerde veilige materialen en productiemethoden waren toen nog niet beschikbaar.
De innovatieve Fully Ceramic Micro-encapsulated (FCM) splijtstof van USNC wordt mogelijk gemaakt door het binderjetten van siliciumcarbide matrixontwerpen om radioactief materiaal te allen tijde veilig ingesloten en ingekapseld te houden.
Desondanks werd de roep om kernenergie geleidelijk af te schaffen steeds luider. Dit terwijl de oprichters van Ultra Safe Nuclear ervan overtuigd waren dat het volledig in de ban doen van kernenergie ernstige gevolgen zou hebben voor de strijd tegen de klimaatverandering en de bestendigheid van wereldwijde elektriciteitssystemen.
Zij besloten daarom om al hun energie en kennis in Generation IV-kernenergie te steken, een nieuwe technologie die hen in staat zou stellen de kernsplijting echt beheersbaar te maken en ongelukken volledig te voorkomen.
Innovatieve aanpak vraagt om innovatieve productie
De kern van een nieuwe reactor ligt besloten in een volledig ingekapselde keramische microbrandstof, genaamd Fully Ceramic Micro (FCM). De productie van dergelijke brandstofcapsules wordt mogelijk gemaakt door de innovatieve 3D binderjet printer van Desktop Metal. Deze printers zijn in staat om hittebestendige siliciumcarbide te verwerken, waardoor unieke 3D-geometrieën geprint kunnen worden die standaard splijtstofdeeltjes veilig kunnen omsluiten.
Vandaag de dag gebruikt USNC de nieuwe productiemethode om hun uiterst betrouwbare en veilige micromodulaire reactor (MMR) energiesystemen van brandstof te voorzien. Aangezien de binder jet 3D printers van Desktop Metal een cruciale stap in USNC's brandstofproductie faciliteren, zijn ze tevens essentieel voor onderliggende innovaties.
Testen in de Benelux
De nieuwe aanpak staat inmiddels volop in de belangstelling. Ook in de Benelux. Zo test de Nuclear Research & Consultancy Group in Petten momenteel de FCM-splijtstof van de USNC.
Eerste microreactor in Canada
Los daarvan werkt USNC, via haar joint venture Global First Power, ook aan de ingebruikneming van haar allereerste MMR in Chalk River Laboratories. Deze locatie is in handen van Atomic Energy of Canada Limited en wordt beheerd door Canadian Nuclear Laboratories. Momenteel wordt getracht een License to Prepare Site te verkrijgen van de Canadian Nuclear Safety Commission (CSNC).
"Kleine reactoren met hun veelzijdigheid en vermogen om schone, goedkope energie op te wekken, zouden de perfecte oplossing kunnen bieden voor unieke energie-uitdagingen, zoals de energievoorziening van afgelegen gemeenschappen en mijnen die momenteel afhankelijk zijn van dure diesel elektriciteit."
-- Todd Smith, minister van Energie.
Over modulaire/microreactoren
- Kleine modulaire reactoren (SMR's) produceren tot 300 megawatt (MW) aan vermogen, terwijl zeer kleine modulaire reactoren (vSMR's) of microreactoren tot 20 MW per module produceren.
- Eén MW levert een jaar lang stroom voor ongeveer 1000 gemiddelde Nederlandse huishoudens.
- Microreactoren zijn gemakkelijk te vervoeren en zullen in de toekomst waarschijnlijk basissen op de maan en Mars van stroom voorzien, alsook de ruimtestations die zich in een baan om de aarde bevinden.
Additive Manufacturing is een hot topic voor veel productiebedrijven. Maar wat maakt 3D printen met de binder jetting-techniek speciaal? We hebben het gevraagd aan Desktop Metal-klant Wall Colmonoy. In deze blog lees je wat zij de 8 belangrijkste voordelen van binder jetting vinden.
1. Hoge snelheid
Met de high-speed, single-pass printtechnologie kan Wall Colmonoy op hoge snelheid hoogwaardige metalen onderdelen produceren. Concreet hebben we het dan over honderden metalen onderdelen per dag. Dit in tegenstelling tot gieten, waarbij het een aantal weken kan duren voordat een onderdeel kan worden geproduceerd. De onderstaande bouwsimulatie voor een pomponderdeel toont hoe honderden onderdelen snel in één batch kunnen worden geprint.
2. Ongeëvenaarde printkwaliteit
Het Desktop Metal Shop System produceert hoge-resolutie onderdelen met ongelooflijk fijne details. Uit de sinteroven komen onderdelen met een oppervlakteruwheid van slechts 4µm Ra. En met nabewerking zijn ruwheden onder 0,1µm Ra mogelijk. Deze componenten zijn massief en hebben een hoge dichtheid waardoor debinding of infill overbodig wordt. Klanten zijn vooral geïnteresseerd in de mogelijkheid om onderdelen te produceren die weinig of geen nabewerkingen vereisen. Dit levert grote tijdwinst en kostenbesparingen op, wat produceren met dit binder jetting systeem met de huidige onzekerheden in de toeleveringsketen nóg aantrekkelijker maakt.
3. Hoge resolutie
Het Desktop Metal binder jet-systeem levert hoge resolutie prints. Met 1600×1600 DPI native, en meer dan 670M drops per seconde, biedt Wall Colmonoy high speed 3D printen met een hoge resolutie voor haar klanten.
4. Flexibele productie
Wall Colmonoy kan op kosteneffectieve wijze kleine series van complexe onderdelen 3D printen door het elimineren van tooling. Ze produceren dagelijks honderden near-net-shape onderdelen met aanzienlijk lagere arbeidskosten en meer geometrische flexibiliteit. Hierdoor kunnen ze snel reageren op de behoefte aan variaties en verbeteringen.
Het in Karnes City, Texas, gevestigde PGV heeft meer dan drie decennia ervaring met het produceren van apparatuur voor de olie- en gasindustrie, lucht- en ruimtevaart, robotica en automatisering. Naast de traditionele productie middels CNC-verspaning, beweegt het bedrijf zich nu in de richting van de next-generation productie door het 3D-printen van metaal op productieniveau te integreren.
De uitdaging
Na meer dan drie decennia onderdelen te hebben geproduceerd met behulp van conventionele methoden – met name CNC-verspaning – voor een groot aantal klanten, is PGV zeer vertrouwd met de uitdagingen waarmee fabrikanten zich geconfronteerd zien.
Gereedschapskosten en doorlooptijden
Traditionele volumeproductie – of dit nu gaat om verspanen, gieten of smeden – vereist harde gereedschappen en bevestigingen die vaak tienduizenden euro’s kosten en weken aan productietijd vergen.
Geen flexibiliteit
Naast het kostenaspect hebben de lange doorlooptijden een significante impact op het vermogen van een onderneming om snel in te spelen op nieuwe of veranderende eisen van klanten. Maakbedrijven worstelen door deze beperkingen met de doorvoer van herontwerpen van onderdelen en nieuwe iteraties van bestaande ontwerpen.
Waar veel van deze bedrijven prototypes in kunststof printen om een juiste pasvorm te testen, vereist het functionele testen het vervaardigen en gebruiken van metalen onderdelen. Dit is een proces dat duur is en veel tijd kost.
Voorraadbeheer
De lange doorlooptijden die inherent zijn aan traditionele productietechnieken gaan ook gepaard met uitdagingen voor het voorraadbeheer. Klanten tijdig voorzien van reserveonderdelen betekent dat producenten grote aantallen reserveonderdelen op traceerbare voorraad moeten leggen, alsook de bijbehorende gereedschappen en toebehoren die nodig zijn om ze te produceren.
Met de groei van 3D-metaalprinten de afgelopen jaren – groei zowel in de mogelijkheden voor complexe functionele onderdelen als in de adoptie door de industrie – zag PGV kansen om elk van deze uitdagingen aan te pakken.
Het Desktop Metal Shop System bleek het ideale systeem om dat te doen.
De Shop System-oplossing
Hoewel minder dan een jaar geleden geïnstalleerd, is de impact van Shop System op de bedrijfsvoering van PGV nu al onmiskenbaar.
Naast het drastisch terugdringen van de kosten en doorlooptijden heeft het systeem PGV in staat gesteld te groeien door het vrijkomen van productiecapaciteit en het vereenvoudigen van het voorraadbeheer. Dit alles leidde tot een flexibelere en efficiëntere bedrijfsvoering.
Bedrijfsgroei
Meer productiecapaciteit, betere dienstverlening
Dankzij toegenomen productiesnelheid door Shop System is PGV veel flexibeler, waardoor het nu ook kleine en middelgrote orders kan aannemen die voorheen niet mogelijk waren door de hoge gereedschapskosten en lange doorlooptijden.
Daar waar er normaliter tot wel vijf processen nodig waren om een boorgat te bewerken, vereenvoudigt Shop System dit proces aanzienlijk, en maakt het tevens ruimte vrij in het machinepark, waar nu andere orders kunnen worden gedraaid.
Het vervallen van de noodzaak voor gereedschappen maakt het gemakkelijk voor PGV om de snelheid van de veranderende wereld bij te benen. Het bedrijf kan bijvoorbeeld het ontwerp van onderdelen snel updaten om aan veranderende klantenwensen tegemoet te komen of geheel nieuwe ontwerpen introduceren zonder de gebruikelijke lange vertragingen die deze bij traditionele maakmethoden tot gevolg hebben.
Het systeem stelt het bedrijf in staat om onderdelen te maken, deze onder echte bedrijfsomstandigheden functioneel te testen en op basis van de bevindingen te optimaliseren. Dit alles in minder tijd dan het zou kosten om alleen al het geharde gereedschap te maken.
Bedrijfsvoering
Terugbrengen fysieke voorraad met 50%
Door de deur open te zetten voor het on-demand produceren van onderdelen stelde het Shop System PGV in staat om haar onderdelenvoorraad met maar liefst 50 procent te reduceren. In plaats van magazijnlogistiek en het beheren van grote fysieke goederenstromen, kunnen ontwerpen nu worden opgeslagen in een ‘digitaal magazijn’ en worden geprint wanneer ze daadwerkelijk nodig zijn.
Tijdbesparing
Terugbrengen doorlooptijden met 50-80%
Met de transitie van verspanen naar binder jetting zag het bedrijf vergelijkbare afnames van doorlooptijden. Orders die ooit tot wel vijf unieke bewerkingsstappen vereisten, werden nu tot één enkele productiestap teruggebracht. Afhankelijk van het onderdeel werden doorlooptijden teruggebracht met minstens 50%, maar ook tot zelfs 80%.
Additive Manufacturing, of 3D printen, verlaagt de kosten, bespaart tijd en verlegt de grenzen van productieprocessen en productontwikkeling. 3D-printtechnologieën bieden veelzijdige oplossingen in een breed scala van toepassingen, van conceptmodellen en functionele prototypes in het geval van rapid prototyping tot mallen, armaturen of zelfs volwaardige eindgebruiksonderdelen vanuit de productie.
De afgelopen jaren zijn 3D-printers met hoge resolutie betaalbaarder, gebruiksvriendelijker en betrouwbaarder geworden. Als gevolg daarvan is 3D-printtechnologie nu voor meer bedrijven toegankelijk, maar het kiezen tussen de verschillende concurrerende 3D-printoplossingen blijft soms lastig.
Welke technologie is geschikt voor jouw specifieke toepassing? Welke materialen zijn beschikbaar? Welke uitrusting en opleiding heb je nodig om te beginnen? Hoe zit het met de kosten en ROI?
In dit artikel gaan we dieper in op de drie meest gevestigde 3D-printprocessen voor kunststof: FDM (Fused Deposition Modeling), SLA (stereolithografie) en SLS (Selective Laser Sintering).
Fused Deposition Modeling (FDM)
Fused deposition modeling (FDM), ook bekend als Fused Filament Fabrication (FFF), is de meest gebruikte vorm van 3D-printen op consumentenniveau, aangewakkerd door de opkomst van hobbyistische 3D-printers. FDM 3D-printers bouwen onderdelen door het smelten en extruderen van thermoplastisch filament, dat door een printermondstuk laagje voor laagje in het bouwgebied wordt gedeponeerd.
FDM werkt met een reeks standaard thermoplasten, zoals ABS, PLA, en hun verschillende mengsels. De techniek is zeer geschikt voor eenvoudige proof-of-concept modellen, maar ook voor het snel en goedkoop vervaardigen van prototypes van eenvoudige onderdelen, zoals onderdelen die normaal gesproken machinaal zouden worden bewerkt.
FDM-onderdelen hebben de neiging zichtbare laaglijnen te vertonen en kunnen onnauwkeurigheden vertonen rond complexe elementen.
FDM heeft de laagste resolutie en nauwkeurigheid in vergelijking met SLA of SLS - en is daarmee niet de beste optie voor het printen van complexe ontwerpen of onderdelen met ingewikkelde kenmerken. Afwerkingen van hogere kwaliteit kunnen worden verkregen door chemische en mechanische polijstprocessen. Industriële FDM 3D-printers gebruiken oplosbare dragers om sommige van deze problemen op te lossen en bieden een breder gamma aan technische thermoplasten, maar ze zijn ook prijzig.
FDM-printers hebben moeite met complexe ontwerpen of onderdelen met ingewikkelde kenmerken (links), vergeleken met SLA-printers (rechts).
Stereolithography (SLA)
Stereolithografie, uitgevonden in de jaren 1980, was 's werelds eerste 3D-printtechnologie en is nog steeds één van de meest populaire technologieën voor professionals. SLA resin 3D-printers gebruiken een laser om vloeibare resin uit te harden tot gehard plastic middels een proces dat fotopolymerisatie wordt genoemd.
Bekijk hoe stereolithografie werkt.
SLA-onderdelen hebben de hoogste resolutie en nauwkeurigheid, de duidelijkste details en de gladste oppervlakteafwerking van alle kunststof 3D-printtechnologieën. Het grootste voordeel van SLA ligt echter in zijn veelzijdigheid. Materiaalfabrikanten hebben innovatieve SLA harsformuleringen van fotopolymeer gecreëerd met een breed scala aan optische, mechanische en thermische eigenschappen die overeenkomen met die van standaard, engineering en industriële thermoplasten.
SLA is een goede keuze voor zeer gedetailleerde prototypes die zeer kleine toleranties en gladde oppervlakken vereisen, zoals mallen, patronen en functionele onderdelen. SLA wordt op grote schaal gebruikt in diverse industrieën van techniek en productontwerp tot productie, tandheelkunde, juwelen, modelbouw, en onderwijs.
Selective Laser Sintering (SLS)
Selective Laser Sintering is de meest gebruikte technologie voor Additive Manufacturing voor industriële toepassingen. Ingenieurs en fabrikanten uit verschillende sectoren vertrouwen op deze technologie voor de productie van sterke, functionele onderdelen.
Bekijk hoe Selective Laser Sintering werkt.
SLS 3D-printers gebruiken een krachtige laser om kleine deeltjes polymeerpoeder samen te smelten. Het niet-gesmolten poeder ondersteunt het onderdeel tijdens het printen en maakt speciale ondersteunende structuren overbodig. Hierdoor is SLS ideaal voor complexe geometrieën, zoals binnenwerkse elementen, ondersnijdingen, dunne wanden en negatieve elementen. Onderdelen geproduceerd met SLS-printen hebben uitstekende mechanische eigenschappen, met een sterkte die vergelijkbaar is met die van spuitgegoten onderdelen.
SLS-onderdelen hebben een ietwat ruwe oppervlakteafwerking, maar vrijwel geen zichtbare laaglijnen. Dit voorbeeldonderdeel werd geprint op een Fuse 1 SLS 3D printer van Formlabs.
Het meest gebruikte materiaal voor SLS is Nylon, een populair technisch thermoplast met uitstekende mechanische eigenschappen. Nylon is licht, sterk en flexibel, en is bestand tegen schokken, chemicaliën, hitte, Uv-licht, water en vuil.
De combinatie van lage kosten per onderdeel, hoge productiviteit, en gevestigde materialen maken SLS een populaire keuze onder ingenieurs voor functionele prototyping, en een kosteneffectief alternatief voor spuitgieten voor beperkte oplage of brugfabricage.
![]()
|
SAMPLE PART Proefonderdeel aanvragenZie en voel zelf de SLS-kwaliteit van Formlabs. We sturen een gratis proefonderdeel naar jouw kantoor. GRATIS PROEFONDERDEEL AANVRAGEN > |
Vergelijking FDM, SLA, en SLS 3D-printtechnologieën
Elke 3D-printtechnologie kent haar eigen sterke en zwakke punten en vereisten, en is dan ook geschikt voor verschillende toepassingen en bedrijven. De volgende tabel geeft een overzicht van enkele belangrijke kenmerken en overwegingen.
FUSED DEPOSITION MODELING (FDM) | STEREOLITHOGRAPHY (SLA) | SELECTIVE LASER SINTERING (SLS) | |
Resolutie | ★★☆☆☆ | ★★★★★ | ★★★★☆ |
Nauwkeurigheid | ★★★★☆ | ★★★★★ | ★★★★★ |
Afwerking oppervlak | ★★☆☆☆ | ★★★★★ | ★★★★☆ |
Verwerkingscapaciteit | ★★★☆☆ | ★★★★☆ | ★★★★★ |
Complexe ontwerpen | ★★★☆☆ | ★★★★☆ | ★★★★★ |
Gebruiksgemak | ★★★★★ | ★★★★★ | ★★★★☆ |
Voordelen | Goedkope verbruiksmachines en materialen Snel en gemakkelijk voor eenvoudige, kleine onderdelen |
Grote waarde Hoge nauwkeurigheid Gladde oppervlakteafwerking Hoge afdruksnelheden Diverse functionele toepassingen |
Sterke functionele onderdelen Ontwerpvrijheid Ondersteunende structuren zijn overbodig |
Nadelen | Geringe nauwkeurigheid Weinig details Beperkte ontwerpcompatibiliteit |
Gevoelig voor langdurige blootstelling aan Uv-licht | Ruwe oppervlakteafwerking Beperkte materiaalopties |
Toepassingen | Snelle prototyping tegen lage kosten Basic proof-of-concept-modellen |
Functioneel prototype Patronen, mallen en gereedschappen Tandheelkundige toepassingen Prototyping en gieten van sieraden Modelbouw |
Functioneel prototype Korte termijn-, brug-, of productie op maat |
Printvolume | Tot 300 x 300 x 600 mm (desktop en werkbank 3D-printers) | Tot 300 x 335 x 200 mm (desktop en werkbank 3D-printers) | Tot 165 x 165 x 300 mm (benchtop industriële 3D-printers) |
Materialen | Standaard thermoplastische kunststoffen, zoals ABS, PLA en diverse mengsels daarvan | Verschillende harsen (thermohardende kunststoffen). Standaard, engineering (ABS-achtig, PP-achtig, flexibel, hittebestendig), gietbaar, tandheelkundig en medisch (biocompatibel) | Technische thermoplasten. Nylon 11, Nylon 12, en hun composieten |
Training | Weinig opleiding in het instellen, bedienen en afwerken van machines; gemiddelde opleiding in onderhoud | Plug & play. Minimale training over opbouw, onderhoud, machinebediening en afwerking | Gematigde training in opbouw, onderhoud, machinebediening en afwerking |
Eisen faciliteit | Omgeving met airconditioning of bij voorkeur aangepaste ventilatie voor desktopmachines | Desktopmachines zijn geschikt voor een kantooromgeving | Werkplaatsomgeving met gematigde ruimtevereisten voor benchtop systemen |
Aanvullende apparatuur | Steunverwijderingssysteem voor machines met oplosbare steunen (optioneel geautomatiseerd), afwerkingsgereedschappen | Wash & Cure (beide kunnen worden geautomatiseerd), afwerkingsgereedschappen | Nabewerkingsstation voor onderdeelreiniging en materiaalterugwinning |
In deze klantcase bespreken we FreeFORM Technologies. Het bedrijf uit de Verenigde Staten levert engineering en productiediensten aan klanten in verschillende industrieën. Als een van de eerste servicebureaus kozen zij ervoor om Additive Manufacturing aan te bieden. Zo kunnen zij voor hun klanten sneller en goedkoper metalen onderdelen produceren.
De uitdaging van FreeFORM Technologies
Er zijn tal van redenen waarom bedrijven investeren in Additive Manufacturing. Bijvoorbeeld het aanbieden van meer mogelijkheden voor klanten of het bijhouden van concurrenten die kansen in 3D printen zien.
Voor Nate Higgins en Chris Aiello, twee van de oprichters van FreeFORM Technologies, was het een beslissing op basis van ervaring. Samen hebben ze tientallen jaren ervaring met Metal Injection Molding (MIM) - ook wel bekend als metaalspuitgieten. Ze kennen als geen ander de voordelen en uitdagingen van dat proces.
MIM is ideaal voor het maken van complexe, kleine tot middelgrote onderdelen in enorme hoeveelheden. Miljoenen of miljarden onderdelen per batch is geen uitzondering. Met als resultaat volledig dichte, isotrope onderdelen met uitstekende oppervlakteafwerkingen. Toch zijn er ook uitdagingen. Vooral op het gebied van tooling, zoals de mallen. Het maken van de mallen voor metaalspuitgieten is duur en tijdrovend.
Om een idee te geven: een enkele mal kan meer dan € 35.000 kosten en het duurt acht tot twaalf weken om deze te maken.
Een ander nadeel is dat je met een mal beperkingen hebt in de vorm. Niet alle geometrieën zijn mogelijk. Kenmerken zoals uitsnijdingen, roosters, organische vormen en niet-ronde gaten zijn te arbeidsintensief (en dus te duur) om ze te rechtvaardigen. En wil je ze toch, dan is er veel nabewerking nodig.
Dat moet beter kunnen, dachten Nate en Chris. En dat kan ook! FreeFORM wendde zich tot de binder-jetting technologie van het Desktop Metal P-1 Production System.
Waarom het Production System ideaal is
Omdat er geen tooling meer nodig is, helpt het P-1 System FreeFORM om aanzienlijke kostenbesparingen te realiseren. Nog belangrijker is dat het Production System de doorlooptijden enorm verkort - in plaats van weken te wachten op de tooling, worden ontwerpen nu direct naar de printer gestuurd.
Een mooi voorbeeld is dat FreeFORM een relatief complex medisch onderdeel produceerde voor gebruik bij kleine chirurgische ingrepen. Bij productie van 1000 stuks of meer was de kostprijs slechts € 5,50 per stuk. En de levertijd bedroeg maar iets meer dan twee weken.
Het produceren van hetzelfde onderdeel met MIM zou resulteren in iets lagere kosten per onderdeel, maar vergde een initiële investering in tooling van meer dan € 35.000. Ook zou het wel drie maanden duren voordat er überhaupt onderdelen konden worden geproduceerd.
De besparingen in tijd en kosten zijn echter nog maar het begin van de voordelen die het Production System. Doordat je niet vastzit aan een eerder geproduceerde mal, kun je het onderdeel simpel en snel verbeteren door de CAD-ontwerpen bij te werken en naar de printer te sturen.
FreeFORM doorbreekt haar eerdere productielimieten met de Production System P-1 printer. Ze produceren nu onderdelen voor een breed scala aan toepassingen, van verpakkingen om persoonlijke verzorgingsproducten in te bewaren tot aan medische apparaten.
Waarom FreeFORM koos voor Desktop Metal
Hoewel de oprichters van FreeFORM uitgebreide ervaring hebben met zowel extrusion als lasergebaseerde metaalprinters, merkten ze op dat beide technologieën uitdagingen hadden. Zo zijn extrusion systemen te traag voor productie in grotere volumes en is lasersinteren erg duur.
“Met Desktop Metal’s P-1 printer waren we in staat om 100 onderdelen in een enkele build te printen, en dat in minder een uur. We konden een bestelling van 5000 onderdelen binnen twee weken printen. Met een doorlooptijd die 20 keer sneller is dan die van concurrerende systemen, was de P-1 een gamechanger voor de flexibele productie van kleine, complexe onderdelen. Ons Production System biedt ongelofelijke productiviteit en we kijken uit naar de release van de P-50.”
-- Nate Higgins, CEO, FreeFORM Technologies
Door de ontwikkeling van binder-jetprinters die hoge snelheden combineren met een hoge capaciteit, zoals de P-1 en P-50, waren de oprichters van FreeFORM van mening dat de technologie klaar was voor commercialisering en de productie van veel eindproducten.
Door de P-1 is FreeFORM veel wendbaarder: onderdelen kunnen snel worden geproduceerd met behulp van een verscheidenheid aan materialen en indien nodig worden gewijzigd. Met de mogelijkheid om een volledige build box in 45 minuten tot één uur te printen, heeft het bedrijf al eens vijf verschillende prints gemaakt in slechts één dag. Tot nu toe heeft FreeFORM geprint met 17-4 en 316L roestvrij staal en hebben ze onderzocht of ze kunnen printen met S7 gereedschapsstaal.
Voorbeelden van producten
Voorbeeld: medische onderdelen
Dit 'pols' onderdeel wordt gebruikt om grijpers vast te houden tijdens minimaal invasieve operaties. Dit onderdeel zou normaal worden gemaakt via MIM vanwege het kleine formaat (slechts 2 gram) en relatief complexe geometrie.
Met behulp van het P-1 systeem was FreeFORM in staat het onderdeel te produceren met een aanzienlijke besparing in tijd en geld. De eerste proefrun van het bedrijf - slechts 50 onderdelen - werd in minder dan tien dagen aan de klant geleverd en het duurde slechts 15 dagen om het aantal op te voeren tot 1000 stuks. Ter vergelijking: de productie van dit onderdeel met spuitgieten zou een doorlooptijd van 12 weken vergen en meer dan € 35.000 kosten aan gereedschappen, bemonstering en inspectie - allemaal vóór er een enkel onderdeel kan worden geproduceerd.
In deze klantcase bespreken we EAC, een bedrijf dat sinds 1992 metalen accessoires maakt voor met name de schoenen- en lederwarenmarkt. De laatste jaren maken ze ook kleine accessoires voor luxe verpakkingen, badkleding en lingerie, cosmetica en meer.
Tegenwoordig is EAC méér dan een bedrijf dat enkel deze metalen sieraden produceert, ze hebben ook een ontwerpstudio waarbij ze nauw samenwerken met klanten om prototypes te ontwerpen en designs op maat te maken.
De uitdaging van EAC Metal Ornaments
Voor luxe artikelen zijn accessoires op maat essentieel. Gepersonaliseerde metalen accessoires zorgen ervoor dat een merk zich kan onderscheiden van concurrenten. Hele productlijnen kunnen zichzelf hiermee positioneren. Daarnaast stralen de metalen onderdelen ook kwaliteit en vakmanschap uit.
Er zijn echter veel uitdagingen in de manier waarop deze luxe onderdelen vervaardigd kunnen worden. Ook is het lastig om aanpassingen te maken in accessoires én deze tegelijkertijd betaalbaar te houden.
Momenteel gebruikt EAC een scala aan productiemethoden, denk aan Zamack-spuitgieten, hot stamping en chemical stamping van messing en de verloren wastechniek. Deze zijn vaak duur en nemen veel tijd in beslag. En kleine ontwerpwijzigingen vereisen de fabricage van nieuwe gereedschappen, wat voor meer kosten en vertraging in het productieproces zorgt.
De hoge gereedschapskosten maken het ook tot een uitdaging om kleine volumes te produceren, want als EAC de kosten per onderdeel laag wil houden, moeten ze duizenden stuks van een bepaald onderdeel produceren om die gereedschapskosten af te schrijven.
Door te investeren in een 3D-metaalprinter, hoopte EAC het beste van twee werelden te combineren: een systeem dat het dure en tijdrovende proces van gereedschap produceren elimineert én in staat is om onderdelen in verschillende volumes te produceren terwijl de kosten per onderdeel laag blijven. Met het Shop System™ van Desktop Metal vonden ze de metaalprinter die dit kon.
Waarom het Shop System ideaal is
Het Desktop Metal Shop System zorgt ervoor dat EAC de ontwikkelingslijnen drastisch kon verkorten: ze kunnen nu in enkele dagen een digitaal ontwerp omzetten in een accessoire, terwijl dit voorheen weken zou geduurd hebben. Het Shop System kan bovendien honderden van deze kleine accessoires metaalprinten in één print job, waardoor het bedrijf de productie van bepaalde accessoires aanzienlijk kon opvoeren.
Sinds de implementatie van het Desktop Metal Shop System, is de productie van onderdelen voor leerproducten gestegen van 10.000 stuks per week tot meer dan 73.000. Het bedrijf kon zo ook in een week tijd 110.600 kleine accessoires produceren, die bijvoorbeeld als tag op lingerie te vinden zijn. Dit proces zou normaal twee weken vergen.
“Het zit in het DNA van EAC om onze klanten creatief ontworpen producten aan te bieden. Met het Shop System kunnen we samenwerken met klanten en de dromen en creatiefste ideeën van onze ontwerpers werkelijkheid laten worden. Additive Manufacturing is de werkwijze van de toekomst voor metalen accessoires.”
-- Patrick Chouvet, CEO EAC Metal Ornaments
In deze blog vertellen we het verhaal van Wall Colmonoy, het bedrijf dat de legering Colmonoy® op de markt brengt. Wall Colmonoy is wereldwijd marktleider op het gebied van superieure hardmetalen legeringen, soldeerproducten, precisiegietstukken en meer. Wall Colmonoy produceert onderdelen die in allerlei sectoren worden gebruikt, van de vliegtuigindustrie tot de olie- en gasindustrie.
De uitdaging van Wall Colmonoy
Vanzelfsprekend heeft elke industrie zijn eigen uitdagingen. Onderdelen die worden gebruikt in de olie- en gaswinning moeten aan volledig andere eisen voldoen (bv. qua sterkte en corrosieweerstand) dan onderdelen die worden gebruikt in minder veeleisende omgevingen, zoals consumentenproducten.
Maar welke producten er ook worden gecreëerd, producenten willen altijd kosten laag houden, doorlooptijden verkorten en downtime minimaliseren.
Om jaarlijks duizenden onderdelen voor zoveel verschillende industrieën te produceren, moet het bedrijf niet alleen een grote voorraad gereedschap en mallen creëren en onderhouden, maar ook snel nieuwe productiehulpmiddelen kunnen ontwerpen, bijvoorbeeld wanneer bedrijven nieuwe onderdelen willen laten produceren of wijzigingen aanbrengen aan bestaande onderdelen.
Om deze uitdagingen het hoofd te bieden en tegelijkertijd de kosten laag te houden en de doorlooptijden te verkorten, koos Wall Colmonoy voor de aankoop van het Desktop Metal Shop System™.
Waarom het Shop System ideaal is
Met het Desktop Metal Shop System™ kan Wall Colmonoy zijn eigen tools produceren: deze kunnen makkelijk 3D geprint worden. Daardoor zijn de productieonderbrekingen, die normaal gepaard gaan met het produceren van gereedschap of het aanbrengen van veranderingen aan bestaand gereedschap via de normale methoden, ook meteen van de baan.
Naast het creëren van tools, zorgt het Shop System er ook voor dat het bedrijf zelf veel sneller antwoord kan bieden op vragen van klanten door zelf snel onderdelen te printen. Het Desktop Metal Shop System™ zorgt voor veel snelheid en flexibiliteit. Als de eisen van een klant voor een onderdeel veranderen, kan Wall Colmonoy hierop inspelen zonder steeds de tools te moeten produceren.
“Deze aankoop is het begin van een nieuw hoofdstuk voor Wall Colmonoy. We zijn geïnspireerd door de mogelijkheden van metaal 3D printen en kunnen hierdoor ons assortiment uitbreiden.”
De technologie van het Shop System staat de technici van het bedrijf toe om meerdere onderdelen te combineren, wat resulteert in meer efficiëntie en betere prestaties van het onderdeel. Met metaal 3D printen kunnen er ook snel onderdelen worden geproduceerd met features die te duur of tijdrovend zouden zijn als deze werden geproduceerd met traditionele methoden, denk aan complexe gebogen oppervlakken, uitsnijdingen en niet-ondersteunde armen.
Daarnaast zorgt Additive Manufacturing er ook voor dat Wall Colmonoy de onderdelen die ze maken voor klanten sneller kunnen aanpassen na een testperiode. Met behulp van het Shop System kunnen ze een aantal versies van een onderdeel printen in één dag en daarna al deze versies testen onder realistische omstandigheden voordat ze een ontwerp definitief maken. En dit allemaal tegen lagere kosten en in minder tijd dan voorheen.
Door het Desktop Metal Shop System kunnen ze ook flexibeler zijn qua inventaris. In plaats van grote aantallen gereedschappen en onderdelen op voorraad te hebben, kunnen ze nu overschakelen op ‘digitale magazijnen’. Hierin worden de bestanden van de ontwerpen opgeslagen. Als een klant een bepaald onderdeel nodig heeft, kan deze op aanvraag worden geprint.
Voordat er werd geïnvesteerd in het Studio System, onderzochten de technici van Wall Colmonoy o.a. laser metaalprinters. Hier ontdekten ze echter enkele beperkingen.
Zo is er veel nabewerking nodig om bouwplaten en print supports te verwijderen. Ook zijn lasergebaseerde systemen relatief traag. Dit resulteert in een langere doorlooptijd en relatief hoge kosten per onderdeel.
Als dit werd vergeleken met het Shop System, zagen ze grote verschillen: met deze metaalprinter kon het bedrijf in een korte tijd veel meer tools en onderdelen produceren.
Een andere belangrijke overweging was het feit dat het systeem gebaseerd is op betrouwbare processen die worden gebruikt in de traditionele poedermetallurgie - met name de processen die worden gebruikt bij metaalspuitgieten (MIM). Omdat de ingenieurs van Wall Colmonoy veel ervaring hadden met poedermetallurgie (en met name het sinterproces) had het bedrijf vertrouwen in het systeem en in het feit dat de ingenieurs het systeem zouden kunnen gebruiken om hoogwaardige, 3D-geprinte onderdelen te produceren.
Het 3D printen van D2 gereedschapstaal. Het kan nu in hoge volumes worden geproduceerd met het Production System™. En dat is goed nieuws. 3D geprinte onderdelen van D2 gereedschapstaal zijn van cruciaal belang voor toepassingen die hardheid en corrosieweerstand vereisen, en daarmee een langere levensduur.
In deze blog maak je kort kennis met 3D printen van gereedschapstaal (D2) op het Production System™ en de voordelen hiervan. Ook zie je een toepassing die 3D geprint is met D2 gereedschapstaal.
Waarom D2 gereedschapstaal gebruiken?
D2 gereedschapsstaal is een veelzijdig, luchtgehard gereedschapsstaal met een hoog koolstof- en chroomgehalte dat wordt gekenmerkt door zijn hoge hardheid en compressiesterkte na warmtebehandeling. Dit gereedschapsstaal biedt ook extreem hoge slijtvastheid, maatvastheid en corrosieweerstand in geharde toestand, een belangrijk voordeel voor conforme koeltoepassingen.
D2 wordt gebruikt voor een breed scala aan koud werk gereedschappen die een combinatie van slijtvastheid en matige taaiheid vereisen. Bijvoorbeeld gereedschapsdelen, stans- en vormstempels, snijgereedschappen voor knippen, polijstgereedschappen en andere slijtageonderdelen.
Wat zijn de voordelen van het 3D printen met D2 gereedschapstaal?
Snel en efficiënt maken
Met de technologie van het Production System™ kun je profiteren van assembly consolidatie. Een volledig onderdeel kan in zijn geheel worden geprint waardoor de arbeidskosten voor de montage aanzienlijk worden verlaagd. Er kunnen duizenden onderdelen tegelijk worden geprint zonder tussenkomst van een operator.
Meer vormvrijheid van ontwerpen
Het Production System™ geeft veel meer flexibiliteit in innovatieve Additive Manufacturing ontwerpen voor de moeilijkste toepassingen. Bijvoorbeeld organische rondingen die de aerodynamica optimaliseren en complexe koelkanalen. Deze zijn vaak onmogelijk om op een traditionele manier te produceren.
Geschikt voor extreme omstandigheden
D2 wordt bijvoorbeeld gebruikt in olie- en gas- of chemische verwerkingstoepassingen vanwege zijn hardheid en corrosieweerstand. Het is een ideaal materiaal voor onderdelen die een extreem hoge slijtvastheid en maatvastheid vereisen.
Wil je maximaal voordeel halen uit Additive Manufacturing, dan zal je ook anders moeten ontwerpen. In deze blog lees je waarom wij - het team van Layertec - dat vinden.
Serieproductie met metaalprinten
Desktop Metal is in 2021 gestart met de uitlevering van het Shop System. Dit najaar komt daar het Production System bij. De twee binder jetting metaalprinters moeten AM-volumeproductie mogelijk maken. Realistische kostencalculaties zien er positief uit. Nu nog de mindset bij de engineers veranderen, want 3D metaalprinten vraagt echt om een andere zienswijze vanaf de ontwerpfase.
Het Shop System
Arnaud Kooij, die vanuit Design Solutions in 2014 Layertec startte, volgt Desktop Metal al jaren van nabij. In 2017 heeft hij tijdens SOLIDWORKS World in Dallas Rick Chin, een van de oprichters, ontmoet. Een paar maanden later was hij bij de officiële lancering van de eerste desktop metaalprinter Studio System in Pittsburgh.
“In 2017 heb ik bij Desktop Metal ook het prototype van het Production System gezien. Daar had ik een goed gevoel bij.”
Nu, vier jaar later, gaat het spel echt beginnen met de komst van de binder jetting metaalprinters.
Het Production System P-50
AM-serieproductie
Samen met de pilot klanten, waaronder BMW, heeft Desktop Metal de binder jetting technologie sinds 2017 verder verfijnd en de machine doorontwikkeld tot wat het nu is: een 3D metaalprinter voor grote aantallen. Inmiddels is hiervan voor toeleveranciers het Shop System afgeleid. Het Shop System is de metaalprinter voor de machinefabriek, de typische toeleverancier van CNC-delen in kleinere series. Dan praat je over een investering op het niveau van een 5-asser.
Het Production System is echt bedoeld voor massaproductie. We verwachten dat het Shop System in de Benelux voor de meeste tractie gaat zorgen. Maar we zijn ook al in gesprek met geïnteresseerden voor het Production System. Voor beide systemen zijn gedetailleerde kostencalculaties gemaakt, waarbij realistisch gerekend wordt met de uren die productiemedewerkers nu bezig zijn met bijvoorbeeld assemblage van onderdelen.
Ook de kosten van het sinterproces, in de eigen oven van Desktop Metal of een industriële sinteroven, worden meegenomen in de simulatie. We willen een realistische simulatie maken. De investeringen in deze systemen zijn te hoog om gebakken lucht te verkopen. De uitkomsten vallen positief uit en het besef dat er een goede business case is voor metaalprinten begint te landen in de markt, getuige het toenemende aantal aanvragen.
Knop moet om
Desktop Metal heeft met beide binder jetting systemen de technologie in huis om AM als productietechnologie voor uiteenlopende toepassingen te gaan inzetten. Nu zal de knop bij engineers om moeten. De denkwijze moet veranderen. Engineers moeten minder in prismatische vormen denken. Om de voordelen van AM volop te benutten, moet je verder kijken dan de enkele component zoals die nu gefreesd of gedraaid wordt. Generative design, topologie optimalisatie en functie-integratie: dat zijn de sleutelwoorden voor de verdere uitrol van AM.
Praktijkvoorbeeld: tandwiel
Zonder een 3D-printer bestaat onderstaand tandwiel uit vijf losse onderdelen. Desktop Metal heeft het voor een potentiële klant op het Shop System geprint. In één geheel, op maat gemaakt voor elke toepassing via een online configurator. Ondanks dat elk product straks uniek is, worden ze in één batch geprint. En assemblagekosten vervallen doordat het product in één keer uit de printer komt.
Men moet naar de mogelijkheden van AM kijken en naar de integrale kosten. Dit geldt voor heel veel toepassingen, bijvoorbeeld voor spuitgietmatrijzen die men kan verbeteren met inserts waarin geoptimaliseerde koelkanalen zitten. De machines zijn er, het materialenportfolio is goed, nu moet men de toepassingen omarmen. Dat zal tijd kosten.
Je kunt de uitrol van 3D metaalprinten vergelijken met de begintijd van de 3D CAD applicatie SOLIDWORKS. Ook toen moest de mindset - “ik teken dat wel even snel in 2D” - veranderen.
Het 3D printen van inconel. Het kan nu in hoge volumes worden geproduceerd met het Production System™. En dat is goed nieuws. 3D geprinte onderdelen van inconel zijn bestand tegen hoge temperaturen en extreme omgevingen.
In deze blog maak je kort kennis met 3D printen van inconel (IN625) op het Production System™ en de voordelen hiervan. Ook zie je een aantal toepassingen die 3D geprint zijn met inconel waarbij uitstekende materiaaleigenschappen en corrossieweerstand een belangrijke rol spelen.
Waarom inconel printen met Production System™?
IN625, een superlegering van nikkel-chroom, wordt gekenmerkt door zijn hoge sterkte, weerstand tegen corrosie en oxidatie, uitstekende lasbaarheid en het vermogen om extreme, verhoogde temperaturen voor onderdelen onder belasting te weerstaan. Het Production System™ produceert onderdelen van IN625 in zeer hoge volumes met uitstekende materiaaleigenschappen.
Het is een essentieel materiaal dat veel wordt gebruikt in lucht- en ruimtevaarttoepassingen bij hoge temperaturen. De corrosieweerstand bij verschillende temperaturen en drukniveaus, maakt het ook een uitstekende keuze voor toepassingen in de scheepvaart, energieopwekking en chemische verwerking.
Wat zijn de voordelen van het 3D printen met inconel?
Snel en efficiënt maken
Met de technologie van het Production System™ kun je profiteren van assembly consolidatie. Een volledig onderdeel kan in zijn geheel worden geprint waardoor de arbeidskosten voor de montage aanzienlijk worden verlaagd. Er kunnen duizenden onderdelen tegelijk worden geprint zonder tussenkomst van een operator.
Meer vormvrijheid van ontwerpen
Het Production System™ geeft veel meer flexibiliteit in innovatieve Additive Manufacturing ontwerpen voor de moeilijkste toepassingen. Bijvoorbeeld organische rondingen die de aerodynamica optimaliseren en complexe koelkanalen. Deze zijn vaak onmogelijk om op een traditionele manier te produceren.
Geschikt voor extreme omstandigheden
IN625 wordt bijvoorbeeld gebruikt in affakkel- en zwavelverbrandingstoepassingen vanwege zijn hoge temperatuur- en corrosiebestendige eigenschappen. Essentieel voor onderdelen die een lange levensduur vereisen. Het is een ideaal materiaal voor onderdelen die een hoge treksterkte en breuksterkte vereisen.
In deze blog vertellen we het verhaal van Ecrimesa Group. Dit Noord-Spaanse bedrijf produceert meer dan 9000 stalen en aluminium onderdelen voor klanten in allerlei sectoren, zoals de auto-, ruimtevaart- en textielindustrie. Ze produceren deze onderdelen met allerlei geavanceerde technologieën, zoals investment casting, MIM (metal injection molding), machining en Additive Manufacturing. Ecrimesa Group is ook het eerste bedrijf wereldwijd dat het MIM-proces heeft geoptimaliseerd zodat de producten worden gemaakt in een oven met katalytische debinding.
De uitdaging van Ecrimesa Group
Elk jaar produceren MIM-leveranciers over de hele wereld miljarden metalen onderdelen voor een lange lijst van industrieën, van autosector tot de ruimtevaart en bijna alles daartussenin.
Hoewel elke fabrikant van dit soort onderdelen met unieke uitdagingen wordt geconfronteerd, zijn er ook algemene uitdagingen die alle fabrikanten hebben. Denk aan hoe je bespaart op kosten, hoe je productieruns versnelt en hoe je productielijnen snel aanpast om de downtime te minimaliseren.
Deze uitdagingen kent de Ecrimesa Group maar al te goed. Met een catalogus van meer dan 9000 unieke onderdelen, is het belangrijk dat het bedrijf een scala aan productie tools heeft om deze onderdelen te maken. Daarnaast is het belangrijk dat het bedrijf snel nieuwe mallen kan maken voor het spuitgieten van metalen onderdelen (metal injection molds) naar wens van de klant.
Zo'n metal injection mold kost normaalgesproken duizenden euro's om te produceren en het hele proces duurt acht tot twaalf weken.
Deze hoge kosten en lange doorlooptijden maken het erg moeilijk om onderdelen snel te produceren, omdat de klant het onderdeel pas krijgt als de mal is gemaakt nadat er tijd en geld werd geïnvesteerd.
Om zo’n mal sneller te kunnen produceren, koos Ecrimesa voor de nieuwste manufacturing technologie op de markt: het Desktop Metal Studio System.
Waarom het Studio System meteen een hit was
De investering van Ecrimesa in het Studio System wierp vrijwel onmiddellijk vruchten af. Met het Studio Systeem kon Ecrimesa mallen printen met vergelijkbare materiaaleigenschappen en oppervlakte-afwerkingen als prototypes die worden gemaakt met MIM. De prints van het Studio System maken zelfs gebruik van dezelfde poeders.
In plaats van het materiaal te injecteren zoals bij MIM wordt gedaan, wordt het materiaal in de 3D printer laag voor laag geprint. De technici van Ecrimesa uploaden simpelweg het CAD-bestand en binnen een paar uur is het onderdeel klaar om geprint te worden.
Dankzij het vermogen om snel onderdelen te produceren, konden de bedrijfsingenieurs een grote verscheidenheid aan prototypes voor zowel nieuwe als bestaande klanten creëren. Ecrimesa gebruikt het systeem ook om delen van prototypes te ontwikkelen die worden gebruikt in sintering tests voor klanten in verschillende industrieën.
Waarom Ecrimesa Group koos voor Desktop Metal
Voordat ze investeerden in het Studio System, werden er verschillende andere 3D printtechnologieën verkend. Er werd zelfs geïnvesteerd in een wax printsysteem om patronen te creëren voor investeringsgieten. En alhoewel dit systeem kon aantonen hoe 3D-printen een aanvulling zou kunnen zijn op de bestaande productiemethoden van het bedrijf, was het beperkt tot het maken van patronen die later nog steeds Metal Injection Molding nodig hadden.
Om een betere oplossing te vinden, verkende Ecrimesa Group 3D-metaalprinten en benchmarkten zij de kwaliteit van verschillende onderdelen, die zij lieten printen door verschillende bedrijven en met verschillende printbenaderingen.
Uiteindelijk kwam Desktop Metal Studio System als beste uit de bus, omdat de onderdelen die met dit systeem geprint waren een superieure dichtheid en minimale vervorming na het sinteren hadden.
PFT IDPro is ontstaan op de middelbare school Lycée Polyvalent Aragon Picasso en heeft als doel zowel studenten als docenten advanced manufacturing skills te laten ontwikkelen. Ze werken nauw samen met lokale bedrijven. Samen onderzoeken zij hoe nieuwe technologieën - zoals Additive Manufacturing - kunnen helpen bij de ontwikkeling van mechatronische producten en systemen.
Wat is de uitdaging van het PFT IDPro?
Het PFT IDPro houdt zich voornamelijk bezig met mechatronica. Dat is een tak van engineering die de disciplines elektrotechniek, werktuigbouwkunde, robotica en telecommunicatie combineert.
Dankzij mechatronica bestaat er een breed scala aan producten en technologieën, van pacemakers tot ‘slimme’ apparaten zoals deurbelcamera’s en robotstofzuigers. Door de stijgende populariteit van mechatronische producten, staan veel bedrijven te popelen om deze tak van engineering te verkennen. Hiervoor heeft IDPro de expertise in huis.
Het delen van deze expertise is niet zonder uitdagingen. Omdat IDPro verbonden is aan een school, is hun eerste missie studenten te helpen vaardigheden te ontwikkelen die ze nodig hebben op de werkvloer. Daarnaast wil IDPro aan bedrijven technische begeleiding én een breed scala aan zelf ontworpen onderdelen bieden om mechatronische systemen te ontwikkelen.
IDPro gaat met het Desktop Metal Studio System beide uitdagingen aan.
Hoe helpt het Desktop Metal Studio System?
Door te investeren in een Studio System is IDPro er zeker van dat studenten hands-on ervaring opdoen met de beste 3D-print technologie. Die ervaring kunnen ze toepassen op de werkvloer. Zo helpt het systeem met de eerste missie.
Ook voor de tweede missie is het Studio System zeer relevant: de zakelijke partners van IDPro kunnen binnen een paar dagen functionele onderdelen voor traditionele productie printen, in plaats van weken - of zelfs maanden!
Het Studio System print onderdelen tegen aanzienlijk lagere kosten dan de andere laserprinters die IDPro heeft. Ook zijn er minder logistieke uitdagingen, zoals het omgaan met potentieel gevaarlijk metaalpoeder. De combinatie van lage kosten en gebruiksgemak zorgt voor een nieuwe productie-omgeving, waarin je veel onderdelen kan printen én testen.
In plaats van één of twee prototypes te maken om je product te testen, print IDPro nu snel meerdere iteraties en verschillende onderdelen met een net iets andere functie of ontwerp. Werkt iets niet? Dan pas je het ontwerp in no-time aan en test je het opnieuw, tot het design precies aan je behoeften voldoet.
Waarom Desktop Metal?
Er zijn verschillende factoren die meespeelden in de beslissing van IDPro om te investeren in het Studio System van Desktop Metal.
Uiteraard helpt het systeem met één van de missies van IDPro, namelijk studenten op verschillende manieren leren werken met geavanceerde productietechnologieën, maar de veiligheid van het systeem was ook een bepalende factor.
Omdat het Studio System niet met losse metaalpoeders of lasers werkt, is de printer ‘kantoorvriendelijk’. Dit elimineert de nood aan speciale voorzieningen of beschermmiddelen. De veiligheid en het gemak maken van het Desktop Metal Studio System een ideale 3D printer voor schoolomgevingen.
Met deze printer kunnen studenten snel hands-on leren metalen onderdelen produceren. IDPro heeft de onderstaande drie voorbeelden gegeven.
Lees in deze blog hoe Partial Hand Solutions de Fuse 1 en Fuse Sift gebruikt om high performance, patiëntspecifieke prothesen te 3D printen.
Partial Hand Solutions (PHS) is opgericht in 2007, met het doel om functionele oplossingen aan te bieden aan mensen met amputaties. Zo bieden ze oplossingen voor actieve soldaten, personen met gedeeltelijke hand- en vingeramputaties en kinderen met uitgebreide prothese-eisen.
Oprichter Matthew Mikosz maakt al heel lang patiëntspecifieke prothesen, maar had altijd één fundamenteel probleem: hoe maak je een duurzame, op maat gemaakte prothese voor een betaalbare prijs?
De uitdaging van Partial Hand Solutions
De afgelopen jaren gebruikte Matthew een workflow waarbij hij injection molding projecten uitbesteedde om prothetische vingers voor patiënten te maken. De onderdelen kwamen dan na 5 weken binnen en werden vervolgens opgeleverd aan de patiënt.
Maar hij wil producten kunnen aanbieden die zorgen voor échte patiëntspecifieke resultaten. In de loop van de tijd heeft hij verschillende technologieën verkend om dat doel te bereiken: van spuitgietmachines tot stereolithografie (SLA) en Fused Deposition Modeling (FDM) 3D-printers. Maar de oplossing vond hij in de betaalbare Fuse 1 SLS-printer:
"Ik heb altijd al een SLS-printer willen hebben, maar die zijn veel te duur voor kleine bedrijven. De Fuse 1 is perfect voor een bedrijf zoals Partial Hand Solutions.” - Matthew Mikosz
Wat is Selective Laser Sintering?
Een Additive Manufacturing technologie die een laser gebruikt om plastic poeder te sinteren in een solide structuur gebaseerd op een 3D-model.
Wat maakt de Fuse 1 anders?
Met de Fuse 1 en de Fuse Sift heeft Matthew de mogelijkheid om hoogwaardige, patiëntspecifieke 3D-geprinte protheses te maken. Voor het eerst kan hij lichtgewicht, duurzame onderdelen printen met een budget dat geschikt is voor een klein bedrijf.
Wat is het verschil tussen de Fuse 1 en andere SLS-printers?
- De efficiënte workflow, die de kosten verlaagt en de ontwerptijd maximaliseert.
- De hoogwaardige materialen.
Matt’s Fuse 1 and Fuse Sift set-up
Efficiënte workflows besparen je tijd en voorkomen frustratie. Daardoor kan je meer tijd besteden aan ontwerpen en minder aan bijvoorbeeld het schoonmaken van onderdelen.
Hoogwaardige protheses 3D printen in 4 stappen
Partial Hand Solutions maakt gecontroleerd te bewegen prothetische vingers op maat. Deze M-Fingers maken ze in 4 stappen.
- Maak je printbestand klaar in PreForm. Preform is de printvoorbereidingssoftware voor Formlabs-printers. Matthew kende dit al, vanwege zijn Form 2 SLA-printers die hij gebruikt voor het maken van prototypes van onderdelen.
“Zelfs als je nog niet eerder een Formlabs-printer hebt gebruikt, is PreForm echt makkelijk in te stellen. Het maakt het eenvoudig om je printbestand klaar te maken.”
- Bereid de Fuse 1 voor. De Fuse 1 wordt geleverd met een ingebouwde preprint-checklist op het touchscreen met geschreven en visuele instructies die elke procedure stap voor stap uitleggen. De eerste stappen zijn het toevoegen van poeder en het plaatsen van een schone optische cassette.
"Na een paar keer door het proces te zijn gegaan, had ik de instructies niet meer nodig. Ik heb het onder de knie gekregen na slechts een paar prints.”
- Poeder recyclen. Fuse Sift doseert en mixt gebruikt en nieuw poeder automatisch, zodat je afval vermindert en grip houdt op je poedervoorraad. Zo produceert Nylon 12 poeder robuuste, volledig functionele onderdelen met een verversingssnelheid van 30%, wat betekent dat gebruikers kunnen printen met tot 70% gerecycled poeder.
“De Fuse en Sift zijn prachtig ontworpen. Je kunt het onderdeel uit de printer nemen, twee stappen zetten en het onderdeel schoonmaken in de Fuse Sift.”
- Verf en monteer de onderdelen. Je kunt de onderdelen verven, lakken, overspuiten, geleidbaar maken door ze te galvaniseren of waterdicht coaten met verschillende kleuren en afwerkingen. De M-Fingers krijgen een mooie zwarte finish dankzij een warm bad in een kleurstofoplossing.
In slechts een paar dagen is de prothese klaar. Dat is een flink contrast met het oude proces dat 5 weken duurde. En omdat je poeder kunt recyclen bij het printen, is SLS 3D printen ook interessant voor kleine bedrijven. De Fuse 1 is ontworpen om maximale doorvoer te bieden tegen de laagst mogelijke kosten per onderdeel.
Het 3D printen van titanium. Het kan nu met het gebruiksvriendelijke Studio System™ 2. En dat is goed nieuws. 3D geprinte onderdelen in titanium hebben een bijzonder grote treksterkte, draagkracht en corrosieweerstand. Ideaal voor hoogwaardige toepassingen in industrieën zoals lucht- en ruimtevaart, defensie, auto, olie en gas. En dankzij de biocompatibiliteit ook bijzonder geschikt voor medische toepassingen, zoals chirurgische apparaten en implantaten.
In deze blog maak je kort kennis met 3D printen van titanium (Ti64) op het Studio System™ 2 en de voordelen hiervan. Ook zie je een aantal toepassingen die 3D geprint zijn met titanium waarbij uitstekende mechanische eigenschappen en corrossieweerstand een belangrijke rol spelen.
Waarom titanium printen met Studio System™ 2?
Het Studio System™ 2 produceert Ti64 met uitzonderlijke mechanische eigenschappen. De onderdelen hebben een vloeigrens van 730 MPa, 845 MPa treksterkte en 17 procent rek. Deze eigenschappen overtreffen de ASTM F2885-17-normen voor metalen spuitgegoten chirurgische implantaten.
Studio System™ 2. Links de printer, rechts de sinteroven.
Wat zijn de voordelen van het 3D printen met titanium?
Snel en efficiënt maken
Het printen van onderdelen in titanium is een prima alternatief voor het machinaal bewerken van titanium. Dankzij de innovatieve Bound Metal Deposition™ techniek (BMD™), kun je sneller en efficiënter een breed scala aan onderdelen voor preproductie en eindgebruik maken. Zonder extra tooling. On demand, gewoon op kantoor.
Meer vormvrijheid van ontwerpen
Studio System™ 2 maakt nieuwe ontwerpen van titanium mogelijk. Denk aan complexe vormen, interne kanalen en lichtgewicht ontwerpen. Deze zijn vaak onmogelijk om op een traditionele manier te produceren. Met 3D printen kun je echter binnen enkele dagen meerdere ontwerpvariaties maken en testen.
Nog sterker en lichter
Ti64 is de meest gebruikte titaniumlegering en heeft een hoge sterkte-gewichtsverhouding. Essentieel voor onderdelen die een lange levensduur vereisen, te maken hebben met extreme omstandigheden of toepassingen waarbij minder gewicht direct zorgt voor betere prestaties.
Wil je nooit onze blogs missen?
/dennie-rijk-spreker-layertec.jpg?width=80&height=80&name=dennie-rijk-spreker-layertec.jpg)